Maxcess opens new facility in India
R&D, Sales, Service and Repair Center will increase customer support for growing market
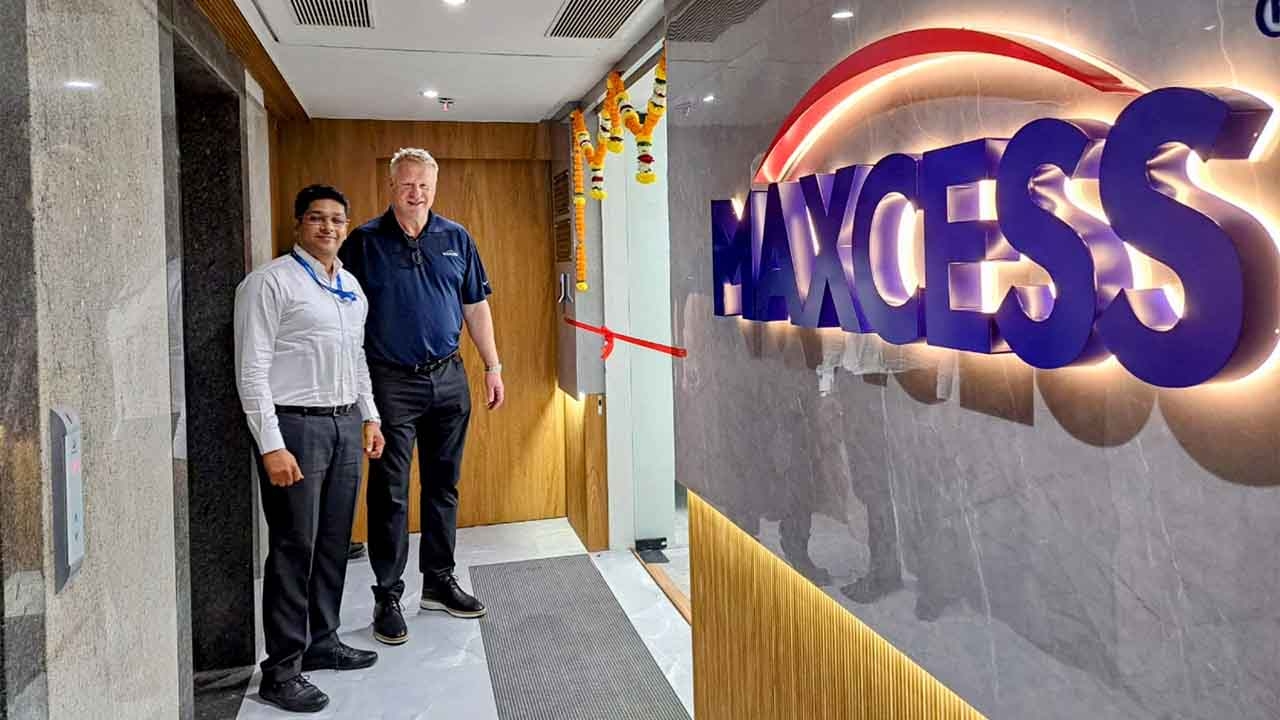
Maxcess International, a manufacturer of automated web handling technology, has opened its new facility strategically located just west of Mumbai.
The facility will house sales and service support, global R&D resources, a repair center, and administrative offices for the APAC region supporting the Maxcess’ portfolio of brands, including RotoMetrics, Fife, Tidland, Magpower, Webex, Componex and Maxcess Vision Systems.
Odd Joergenrud, CEO of Maxcess, said: ‘I wanted to be here to celebrate this important Maxcess milestone and we are thrilled to invest in our new Maxcess R&D, sales, service and repair center in Mumbai. India and the Asia Pacific market are of great strategic importance to Maxcess, and this expansion allows us to bring our industry leading end-to-end web handling solutions to more people in the region. Additionally, adding to our global R&D team locally brings us closer to our customers to create even better solutions. With this facility, we aim to further enhance our sales and technical support, improve regional response time, create new innovations, and achieve greater productivity and efficiency for our customers.’
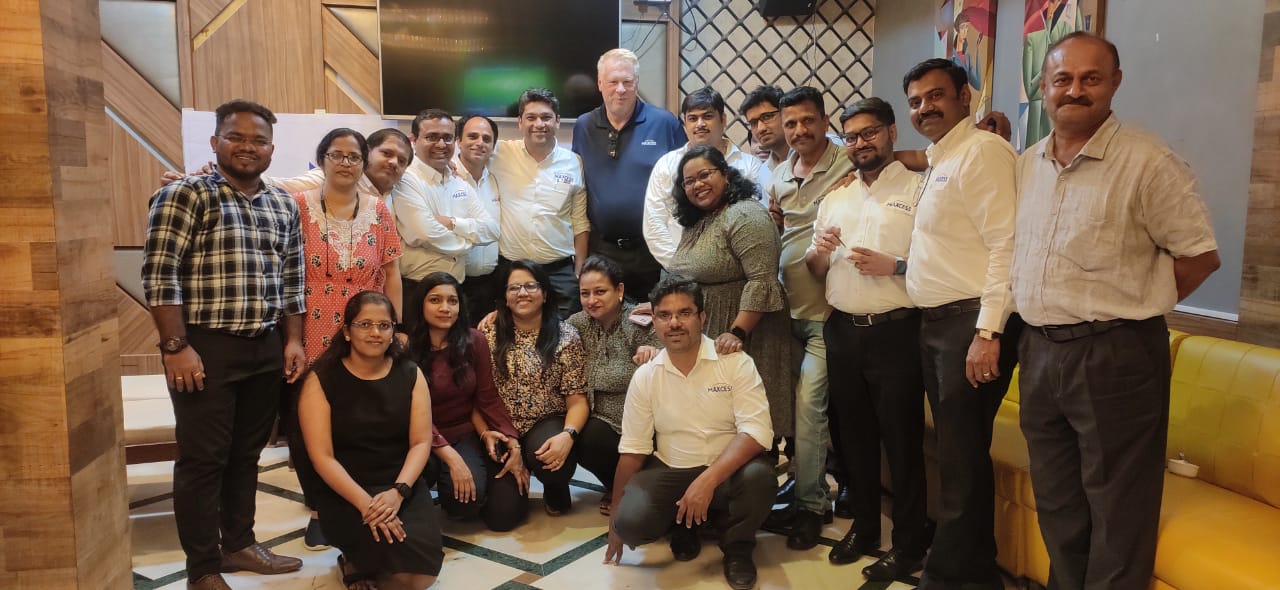
The new multipurpose facility is designed with a focus on delivering its services to the Maxcess customer base. The new offices will have over 30 dedicated employees for the India and Asia Pacific region. Equipped with the latest technologies and staffed by skilled professionals, the facility is poised to meet the growing demands of the region’s web handling segments, including printing, tag and label, packaging, medical, towel & tissue, tire and rubber, metals, and other converting applications.
Niraj Muni, general manager of Maxcess India, said: ‘The Mumbai R&D, Sales, Service and Repair Center will offer a wide range of services tailored to meet the needs of customers in the region. Our customers will notice faster turnaround time on repairs, increased tooling efficiency and durability, which reduces scrap and waste to be more sustainable, improved technical and support in the places our customers do business. I am excited to help Maxcess grow in this important part of the world.’
By combining Maxcess’ extensive product portfolio with customer service experience, the center will function as a hub for collaboration, innovation and knowledge sharing in the region.
Stay up to date
Subscribe to the free Label News newsletter and receive the latest content every week. We'll never share your email address.