PrintCYC develops printed plastics recycling technology
Circular economy initiative PrintCYC has developed a cost-effective technology to recycle up to 100 percent of printed plastic films into high-quality recyclates comparable with virgin materials.
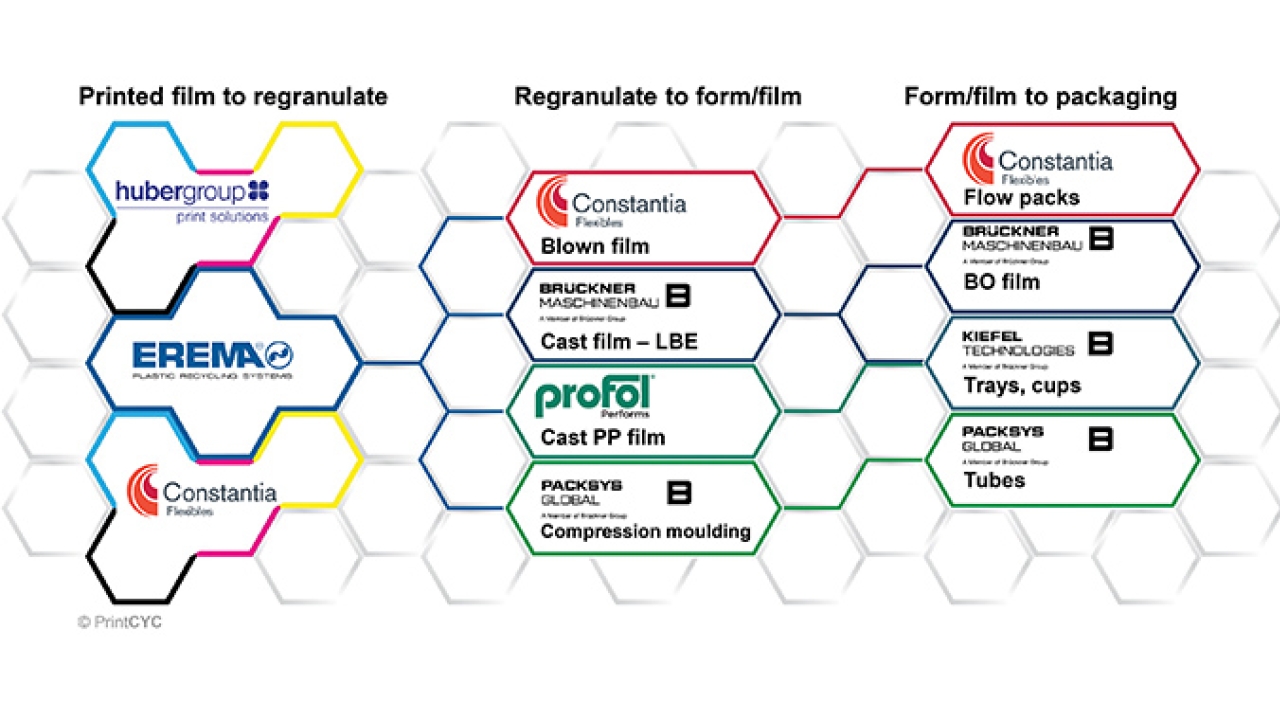
PrintCYC is a value chain initiative for the recycling of printed films, founded in March 2019. The acronym PrintCYC stands for printed polypropylene (PP) and polyethylene (PE) films for mechanical recycling.
Current members are the machine suppliers Brückner Maschinenbau, Kiefel and PackSys Global, a CPP film specialist Profol, an ink manufacturer hubergroup, converter Constantia Flexibles as well as the recycling technology specialist Erema. The initiative is coordinated by Annett Kaeding-Koppers as independent packaging and sustainability consultant.
The project group has achieved remarkable results regarding the recycling of printed plastic films and processing of recyclate. Project members joined forces to research and test new ways for creating circular economy technologies based on post-industrial waste from printed plastic films in the most cost-effective manner. Deinking technology was not considered within this project.
In phase 1 of the project, PP film and packaging samples were successfully produced with more than 50 percent of PP recyclate. The base material was printed biaxially oriented PP (BOPP) films on nitrocellulose (NC) based ink formulations. Nevertheless, the recyclate quality was not completely satisfying regarding material properties like color, smell and processability.
Based on the results from phase 1, PrintCYC members experimented with further improvement by testing alternative ink formulations for printing on BOPP and Low-Density Polyethylene (LDPE) films. Switching to a polyurethane (PU) based ink system in flexo printing in phase 2 resulted in significant improvements of the mechanical recycling process on a production line, which is typically used for reprocessing printed film waste materials in practice.
Due to the inks' high-temperature resistance, neither volatile by-products nor odor or gels were observed, leading to a new class of premium-quality recyclates, showing cooler stable properties. A first environmental impact assessment showed decreased greenhouse gas emissions due to lower energy consumption of mechanical recycling of LDPE films compared to virgin material production.
The new premium recyclates showed excellent processability for blown films, cast films and even biaxially oriented films, which were 100 percent comparable to virgin material.
The EU Plastics Strategy strives to increase the number of recyclates in plastic products and packaging. Within the PrintCYC project, the impact of recyclate reuse in different packaging formats was also evaluated. In phase 2 of PrintCYC, packaging formats such as flow packs, trays, yogurt cups and tubes have been produced, proving usage of rPP and rPE recyclates in processes such as sealing, thermoforming and compression molding.
Currently, PrintCYC members are presenting the results to further value chain stakeholders to exchange expertise and eventually win new project partners. Another objective is to use the results for further development of Design for Recycling Guidelines. The next steps on PrintCYC’s sustainability journey towards a circular economy will be defined in the following weeks.
Stay up to date
Subscribe to the free Label News newsletter and receive the latest content every week. We'll never share your email address.