Alyaska-Poligrafoformlenie invests in second MPS press
Russian converter, Alyaska-Poligrafoformlenie, has invested in a 10-color MPS EFA 430 fully automated flexo press to expand its overall production capabilities.
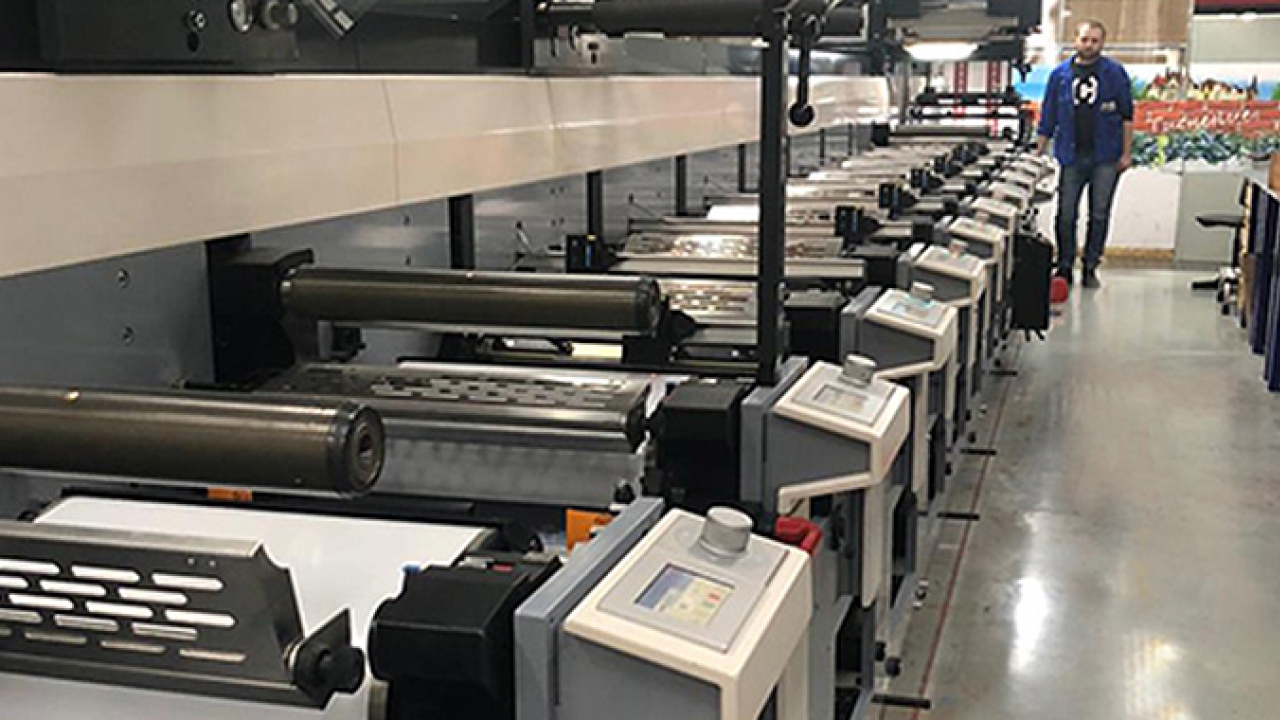
The company, founded in 2003 from a merger of the Alyaska-Print company and the Poligrafoformlenie holding, produces all types of self-adhesive labels, flexible packaging, shrink labels, thermal tickets, stickers, and other products serving the alcoholic beverages, food, cosmetics, household chemicals, and other end-user markets.
The production is spread across two sites operating more than ten flexographic presses, two gravure printing machines, two digital presses, laminators, thermal printers, and a large fleet of finishing equipment.
Alyaska’s first 9-color MPS EF 430 press was installed in 2017, adding to the fleet of narrow-web presses from Mark Andy and Gallus. Successful experience from the two-year operation led Alyaska's management to the second investment in the Dutch-made machine.
The latest new MPS EFA 430 10-color press installed at Alyaska, led by Ogard, the Russian representative of MPS Systems, is a high-performance and highly automated servo-drive printing and finishing system. It is equipped with UV and air dryers, a rail-mounted multi-lamination unit, and de-lam/re-lam, a web-turn bar, and screen-printing modules.
Mikhail Belousov, CEO of Alyaska-Poligrafoformlenie, commented: ‘Investing in a second MPS machine gave us a good opportunity to replace our old printing equipment for a much more efficient and productive environment. For example, with our two MPS printing presses, we can print twice as fast as before while maintaining high quality. This is also supported by video control systems installed on both machines. As a result, our investment in a second MPS was influenced by our extremely positive impressions of the first MPS in terms of high print quality, overall performance, automation, and waste reduction.
‘And of course, the interchangeability in tooling and rearrangement of print jobs between machines is an additional advantage. Our first MPS machine absolutely works without any complaints, and we are very satisfied with Ogard’s high-skilled service team. We optimized our portfolio of jobs, and the efficiency of work shifts increased by 25 percent. Therefore, the logical step was the investment in a second machine from the same manufacturer.’
All printing units on Alyaska’s latest MPS press are equipped with a fully automated print control system, including automation on the print sleeve settings on the print gap, slide-out ink drawers, and the innovative MPS Dynamic Print Control technology for consistent print quality. Another interesting feature is a hot air-drying system. This allows the use of water-based inks in one of the sections, in which an additional air-drying chamber is installed with a continuous supply of hot air.
‘As for the capabilities, we opted for the maximum level of automation with our latest MPS EFA machine,’ added Belousov. ‘This allows fastest changeover time with the lowest amount of waste. Also, I would mention the very attractive price offered by MPS. We are happy with our new machine, which allowed us to immediately transfer all key jobs to both MPS machines - they are now the driving force of our flexographic production.
‘Our company has worked with the largest Russian brand owners for more than 15 years, which have the highest quality requirements for its label and packaging products. Our investment in a second MPS machine with the highest level of automation allows us to produce premium labels with various configurations and with the highest quality that all our customers expect.’
Stay up to date
Subscribe to the free Label News newsletter and receive the latest content every week. We'll never share your email address.