Blair Labeling Inc. installs new MTR turret rewinder
Blair Labeling Inc. located in Denver, Colorado has recently installed a MTR series turret rewinder from KTI.
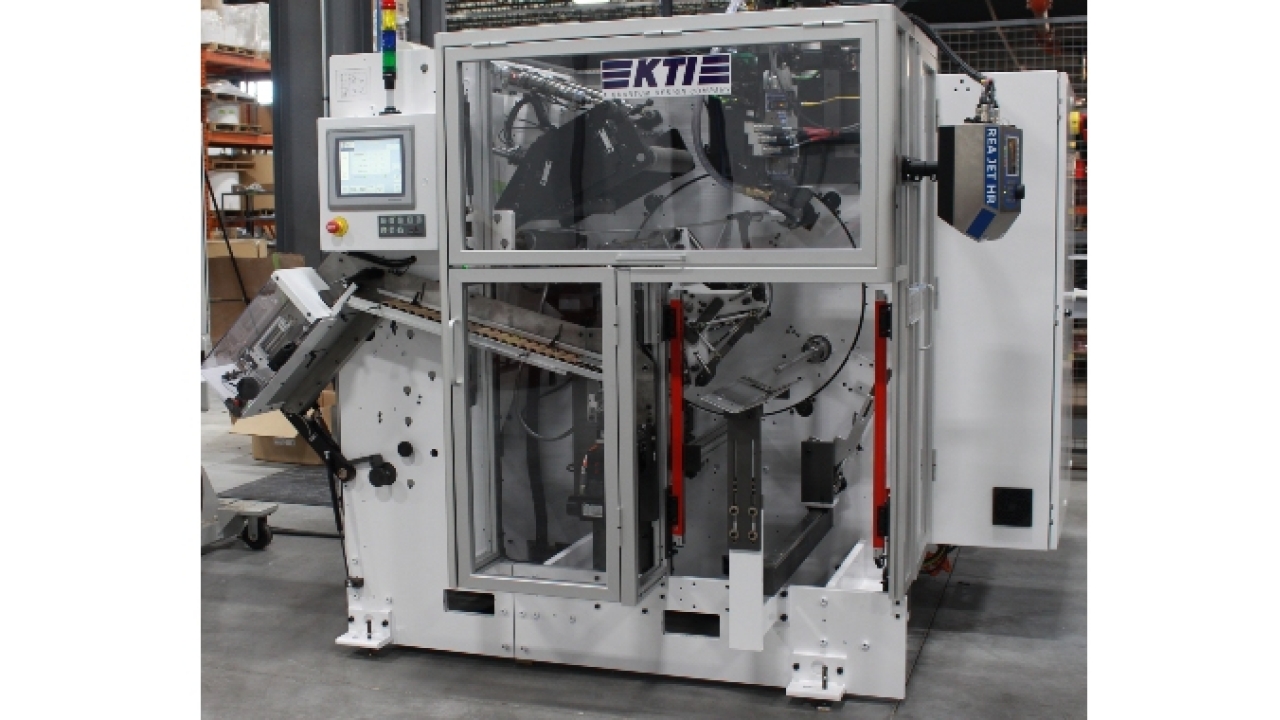
Blair Labeling Inc., a small family-owned, double-minority owned and female owned business, founded in 1987 is a full-service, pressure-sensitive label printing company that creates premium labels, tags, and specialty products. Blair was looking for a solution to increase its production times, reduce the amount of time it took to finish projects on its press, and speed up the finishing process. Blair chose KTI based on the company's reputation and the fact that KTI was highly recommended from other converters in the industry.
Blair Labeling is running a 54# semi-gloss with an all temp adhesive on a 40# SCK liner. Blair specifically chose the MTR Turret Rewinder to increase production. With one of the primary focuses being speed, the MTR will allow Blair to meet its customer satisfaction goals and deliver orders quickly. Prior to purchasing the MTR, Blair was getting a 10,000 to 12,000 machine count in a 10 hour shift through the existing rewinder because of the labor intensive work required. With the new MTR series turret rewinder Blair is consistently getting a 40,000+ count through the machine in less than 6 hours time.
‘The biggest issue we have now is boxing finished rolls fast enough because the machine runs so efficiently and is consistent. Not only were we able to get a project done in less than a week but we were also able to deliver the project two days early with a three day transit time included, something we had not been able to accomplish until this point,’ said Marco De La Vega, CFO of Blair Labeling.
According to the company, the MTR is the perfect fit for Blair Labeling, as it has increased production speeds leaving more time for the operator to focus on machine efficiency and package finished rolls. The automatic tail gluer closes rolls leaving them ready-to-package right off of the machine. With the MTR’s small footprint, it can be seamlessly integrated into most production lines.
De La Vega added, ‘if someone were to ask me what is one regret about purchasing the machine, it would be that we didn’t buy it sooner. It amazed us how much of our work “qualifies” to run on this machine and make our operation that much more efficient. It has taken something that was a pinch point in our operation and made it a non-issue. Our mentality has shifted from thinking how we can get a job on a press sooner to accommodate the rewind time, to now focusing on getting more work to keep this turret running non-stop.’
‘Our goal with each order and customer is to provide a solution to a specific problem,’ said Robin Sherlund, regional account manager for Blair Labeling, at Quantum Design Inc. ‘With a customer like Blair, they knew exactly what problem needed fixing, and we had a great solution to offer them in the MTR series turret rewinder.’
The MTR series turret rewinder has four spindles and is available in web widths up to 22 inches (558mm), roll diameters up to 16 inches (406mm), speeds up to 750FPM (228MPM) and can run cores ranging from .75 inches to 3 inches (19mm to 76mm). Standard features include PLC touch screen controls, servo motor driven spindles, an integrated dancer for superior web control, tapered winding tension, and finished roll removal.
Optional features available for the MTR series turret rewinder include upgrading the roll closure system to add optional print and apply functionality, automatic core loading with adjustable spacing of cores, proprietary core hopper system that handles cores sizes from .75 inches to 3 inches, and a slitting module. Customers can choose from two types of core gluing: an automatic spray glue system with a hot melt tank and spray nozzle, or the traditional hot melt glue pot with an optional refill system.
Stay up to date
Subscribe to the free Label News newsletter and receive the latest content every week. We'll never share your email address.