Country Products invests in Allen Coding thermal transfer printers for productivity
Country Products has invested in NGT2 and NGT4 thermal transfer printers from Allen Coding in order to cope with extra capacity and minimize machine downtime.
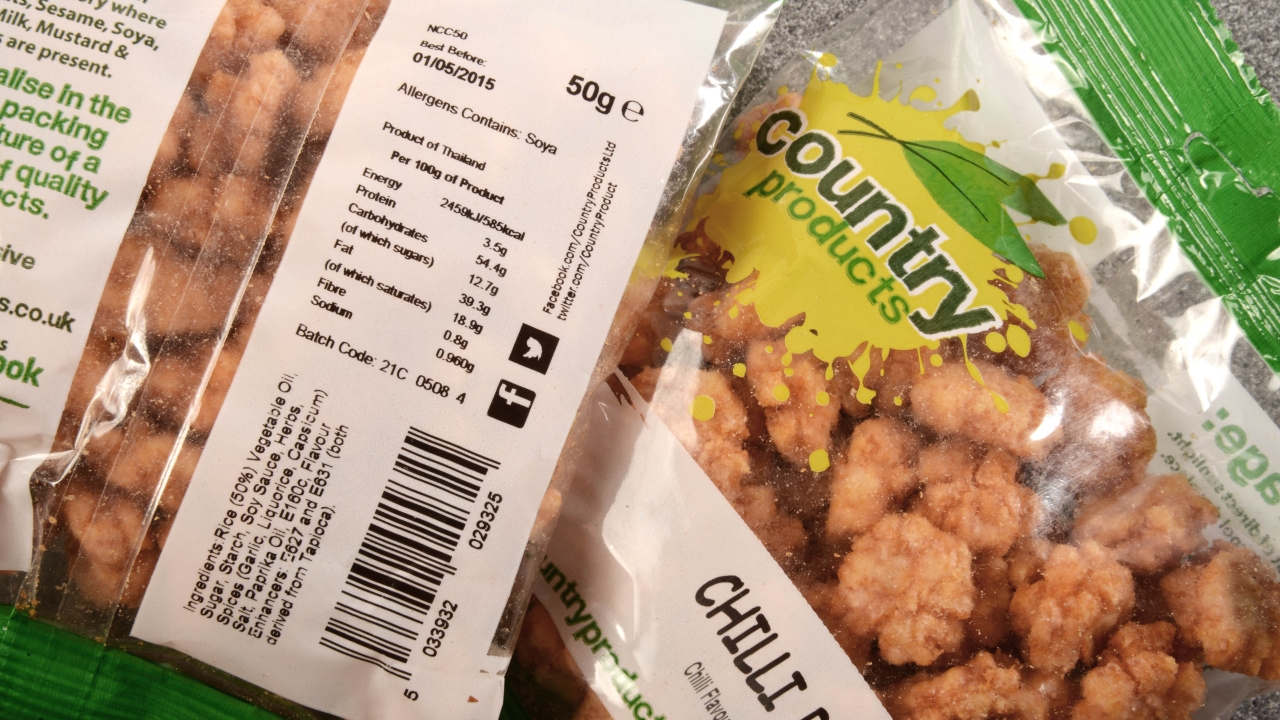
Country Products is a packer of dried foods and snack products, supplying independent traders under its own brand and also providing contract packing for clients throughout the UK.
Country Products has invested in two different models from Allen Coding’s NGT Series to enable it to apply data sets on both the front and rear of generic packaging film produced from polypropylene, polyester or laminate. The printers also apply vital product and nutritional details in line with the company’s commitment to meeting all new food information regulation requirements.
A wide variety of products are being handled by the vertical form fill seal machine, with packs ranging from 15g to 500g in weight. As a result, the Allen Coding NGT2 and NGT4 printers are operating at speeds up to approximately 30 packs per minute.
The investment has been made as part of an upgrade to Country Products’ production line at its plant in North Yorkshire, with the two thermal transfer printers mounted on a special frame at the rear of Country Products’ Gainsborough vertical form fill seal machine. The units are installed on 90-degree swivel brackets so that they can be turned by the operator, both to change thermal transfer ribbons and to move swiftly from one orientation to another for different client films. New mounting bars were also fitted onto existing brackets so Country Products was able to raise the height of the printers on the machine.
Nigel Robertshaw, technical and site manager at Country Products, said: ‘We have previous experience of using Allen Coding printers so it was a natural progression to look at new systems from them.
‘As well as offering the print area specifications required, the NGT2 and NGT4 thermal transfer printers provided significant print quality and performance benefits and were able to meet all our client packaging variables. Plus both models were compatible with our older printers so there was no need to update the labeling software.
‘Production efficiencies have increased as there is less downtime as a result of printer faults. It was vital that the new printers offered reliable performance especially as we are now running an evening shift and have limited engineer cover outside of normal working hours.’
Stay up to date
Subscribe to the free Label News newsletter and receive the latest content every week. We'll never share your email address.