Kumar Labels upgrades all flexo presses from conventional to UV LED
Kumar Labels (KL), recently incorporated under Spirited Labels, has moved all its flexo presses from conventional UV to LED-UV. The company has also invested in two high-speed die cutters, a pre-owned Esko CDI, a new 350m/min speed jumbo slitter, a double camera-based vision inspection system, a sleeving line for short-run embellished shrink sleeves and a camera-based plate mounter.
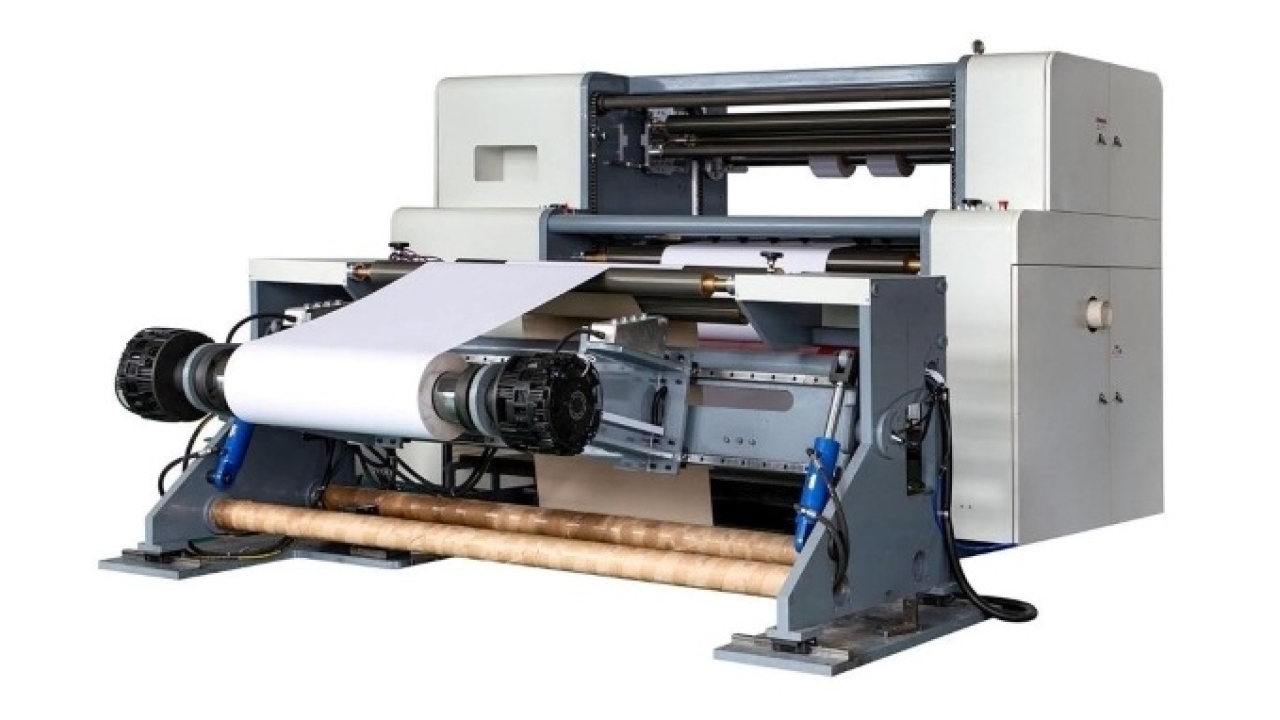
Overall, the company spent over half a million dollars to strengthen the relationship with customers and to invest in machines for better productivity and sustainability.
Anuj Bhargava, CEO of Kumar Labels, said: ‘I have been exploring UV LED for a few years. During casual discussions, most would reluctantly comment that it is not quite a mature technology and that no one has installed it much.
‘In December 2019, I visited Labelexpo China and noticed that all machine makers were selling machines with LED UV only. I visited a factory that had been running on LED UV for the past five-plus years. The cost of inks and varnishes were the same or sometimes even less than conventional inks. That day I set a target to convert all our machines to LED within two years. We did it in much less time.’
The new LED UV systems save 60-70 percent power.
Bhargava added that he personally took clamp meter readings and found that a 6-color conventional system consumed 82Amps and LED consumed just 33Amps. That’s a straight 60 percent cut. More than that, there are zero emissions from LED UV since no air blowers are sucking out heat and ozone generated during arc lamp curing.
‘Cooler press rooms require less air-conditioning. As LED inks require less lay down, press speeds are pushed up by at least 20 percent. In our case, it is actually higher. The standard life of UV LED is more than 20,000 hours which is about 10 times the life of an arc lamp. So, you consume less energy, emit less, dispose less mercury, increase productivity and reduce your replacement costs,’ he explained.
Other investments include two new high-speed die cutters (two were previously installed in 2020) that can do flatbed die cutting at 400 impressions per minute. This reduces dependency on expensive rotary flexible dies especially in uncertain courier delivery times.
A pre-owned Esko CDI has been installed to support in-house platemaking for the company’s multiple sites. Bhargava calls it a ‘hub and spoke’ model. McDermid Lava thermal processor is on its way for solvent-less plate processing – yet another step towards sustainability.
A new 350m/min speed jumbo slitter would complement KL’s new hot-melt labelstock line and support the existing acrylic coater. The labelstock unit can support multiple plants making investments in a new coating and slitting lines necessary.
As the labelstock and printing productivity increases, finishing capacity needed to be increased. For this KL has added a new double camera-based vision inspection system. This device can detect all texture, embossing and screen-printing defects apart from the usual defect detection capability.
A sleeving line for short-run embellished shrink sleeves and a camera-based plate mounter for better mounting accuracy of plates were also a part of the new investments.
Apart from the above investments, the Nepal unit of Kumar Labels is expected to be commissioned by June 2021.
Stay up to date
Subscribe to the free Label News newsletter and receive the latest content every week. We'll never share your email address.