Moquin Press installs Heidelberg’s first 21K Speedmaster XL 106
The XL 106 has increased Moquin Press’s label net output by 18 percent and plays a vital role in the company’s sustainability efforts.
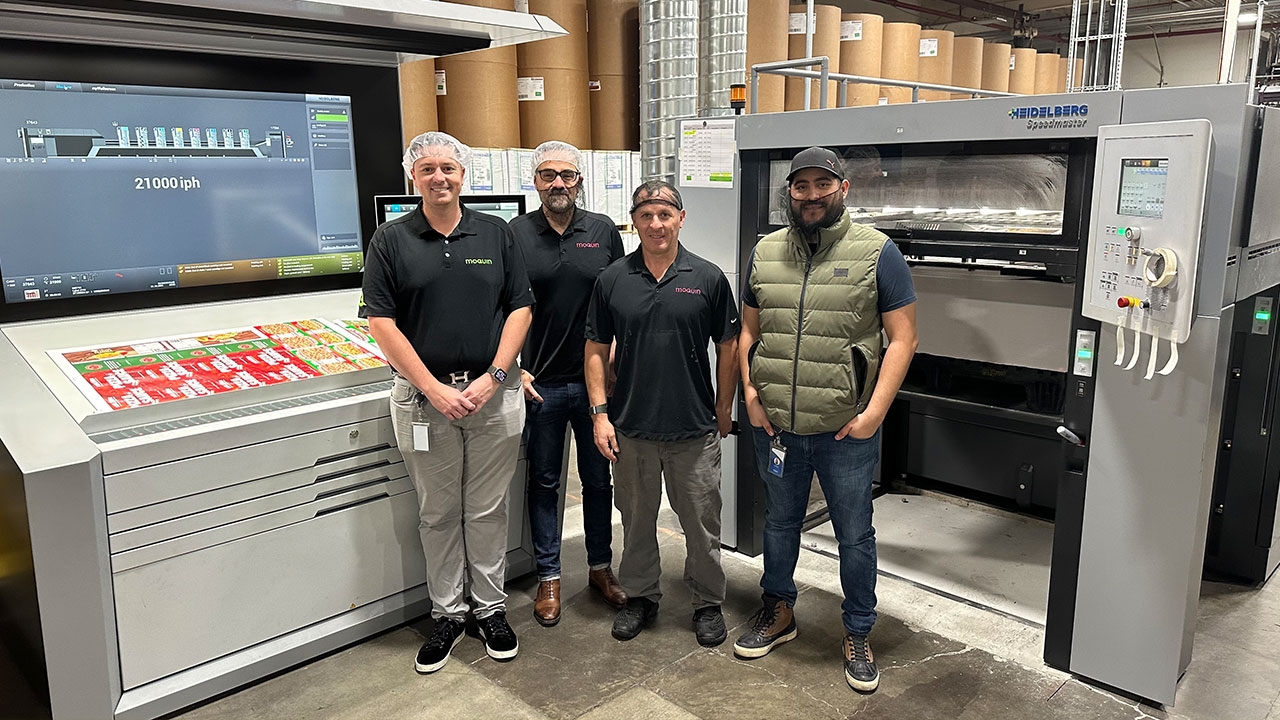
L-R: Bryan Moquin, business development manager; Marcio Ribeiro, general manager; Danny Robertson, production manager and Jayro Molina, finishing department manager.
Moquin Press, a US-based print and packaging provider has installed a new Speedmaster XL 106 from Heidelberg to cut and stack labels. It is the first in the United States to print 21,000 sheets per hour and the first in world specially designed for label production.
Equipped with the newest generation Prinect Inpress Control and CutStar in-line sheeter, the XL 106 has increased Moquin Press’s label net output by 18 percent and plays a vital role in the company’s sustainability efforts.
Its newest machine is part of Moquin Press’s XL Legacy, having also been the first in the US to install both the Speedmaster XL 105 and XL 106 with push-to-stop technology.
Moquin Press’s business has significantly evolved since it installed its first XL 105 in 2004. The company has made almost a full transition to packaging – now specializing in folding cartons and cut and stack labels.
‘We started looking closer at the industry trends and the needs of our target market,’ said Bryan Moquin, business development manager at Moquin Press. ‘We then decided to focus all of our investments in the last two years on developing these two product lines.’
Moquin Press made its first steps to solidify its presence in the food packaging market in 2021 with the acquisition of Valley Printing, a cut and stack label printing company recognized for having a large footprint in the Central California food industry.
The recent investment is the first Speedmaster XL 106 in the US rated for printing 21,000 sheets per hour. The 7-color press with in-line coating replaces an older XL 105 and is equipped with Heidelberg’s latest innovations, including autonomous push-to-stop technology, AutoPlate Pro, and the Heidelberg User Experience.
Moquin Press’s 21K model is the first in the world specifically developed for the requirements of high-performance label printers. It includes changes to the CutStar and special sheet travel adjustments in the units and the delivery, which are optimized for thinner materials.
‘Since its inception, the Speedmaster XL press family has undergone a remarkable evolution across various domains,’ said Marcio Ribiero, general manager for Moquin Press. ‘Among its notable advancements is the ability to seamlessly operate at peak speeds across a broad spectrum of substrates. The print quality it delivers is exceptional, embodying a machine engineered for longevity.’
The new press was installed late last year, and since production started, the machine consistently runs at top speeds, 24 hours a day across three shifts. Its enhanced automation and built-in artificial intelligence mean the press requires significantly less manpower than the company’s previous press.
With Intellistart 3, all the steps required for job changes are defined without any operator intervention for all active and queued processes.
‘Not only is the press incredibly consistent and stable during the run, so many of the processes are automated, and the technology is so intuitive. It’s the best Speedmaster we’ve ever had,’ added Moquin.
‘Our latest investment is a testament to our dedication to both quality and sustainability,’ commented Juliana Lopez, marketing director at Moquin Press. ‘We believe businesses have a responsibility to minimize their environmental impact. This press is a significant step in that direction.’
By increasing net output, Moquin Press can produce more units in less time, lowering its overall energy usage. Additionally, the new XL 106 is a carbon-neutral press, which means CO2 emissions that are generated during press production are compensated for by HEIDELBERG purchasing climate protection certificates (Gold Standard).
‘Being able to rely on the Heidelberg service team has been the driving factor for a lot of our decisions. They’ve always stood behind what they said they were going to do. Heidelberg has always been a great partner to us,’ concluded Moquin.
Stay up to date
Subscribe to the free Label News newsletter and receive the latest content every week. We'll never share your email address.