TQL installs Nilpeter FA-26 with E-Beam
Texas-based converter TQL Packaging Solutions (TQL) has invested in Nilpeter’s multi-faceted, in-line FA-26 flexographic press to strengthen its market position in short-run flexible packaging segment.
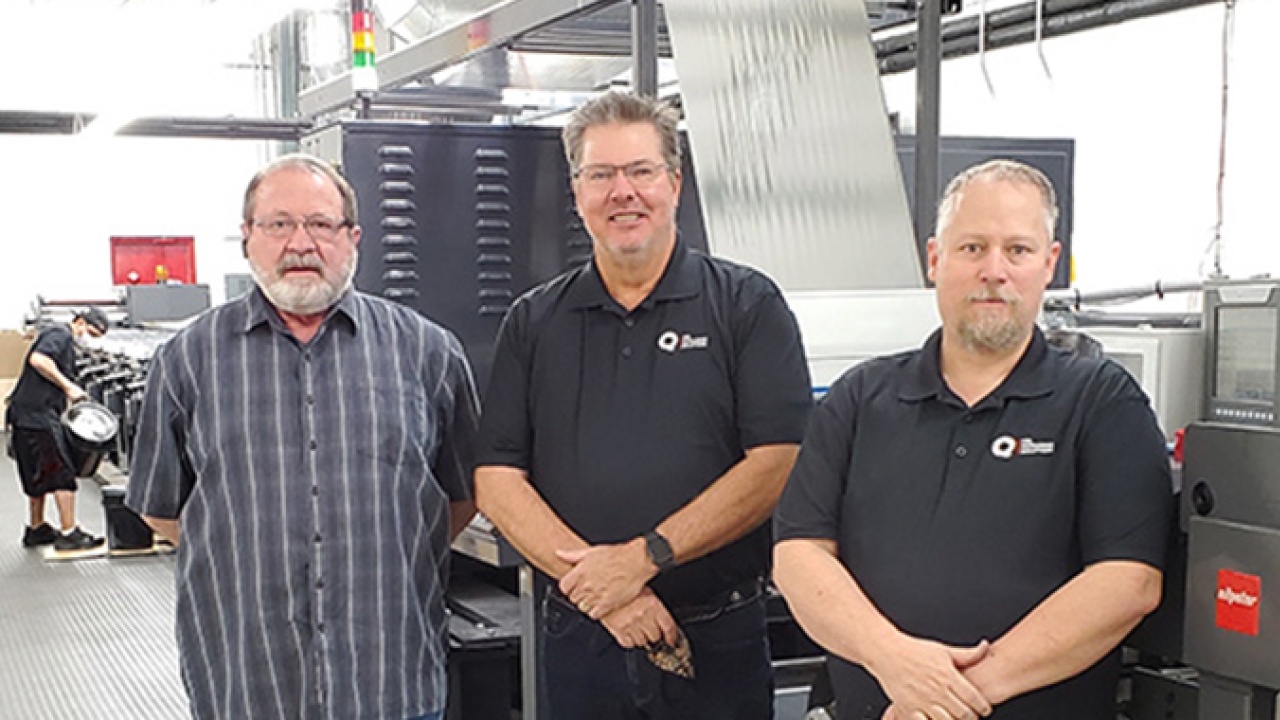
The FA-26 is the widest press released to the global market to date by the Danish manufacturer, and the TQL installation is the first of Nilpeter’s press series to include in-line E-Beam lamination. With 10-color stations, UV-LED curing lamps, and UV and E-Beam capability all in-line, it has been designed to maximize the profitability of short-run conversion of film structures for pouches, sachets, stick packs and shrink sleeves.
The FA-26 carries the same features and benefits the Nilpeter brand is regarded for in the narrow web printing market combined with broader throughput and a new printhead design supported by comprehensive and advanced automation systems.
‘It is rare for a piece of equipment to exceed my expectations,’ said Scott Smith, TQL Packaging Solutions founder. ‘I knew the Nilpeter FA-26 would be a great press, but it has delivered beyond what I expected in performance. ‘We’ve done well to jump to 26in. At this width, we’re able to address a piece of the market that we had not been wide enough to service previously.’
The increased width has dramatically improved the converter’s hourly throughput. Additionally, the wider web brings greater opportunity to capture new business in several popular formats and designs that require a printing web greater than twenty inches.
The FA-26 features a new landscape printhead design to the in-line flexo machine that supports the execution of premium print quality across the additional web width. Eight motors drive and control each printhead with closed-loop feedback to the PLC.
‘Nilpeter’s technology in the FA-26 has jumped from previous films presses. The landscape design of the printhead is awesome. It greatly minimizes the bounce that some images produce on our traditional film presses, and it allows us to increase speed,’ added Smith.
TQL is running jobs at or below 25,000 feet, setting up faster than its narrower equipment with set-up automation, and doubling the speeds it regularly runs on 16in presses. With job memory and auto-register, TQL operators can efficiently web the press and dial-in settings to produce saleable product quickly with less waste and higher quality.
‘We are noticing far better efficiencies in set-up, and less waste, even with a much wider web than we’re used to running,’ said Smith. ‘There’s a huge number of buyers out there that want the super high quality and consistency that they’re used to getting from gravure. This new press allows us to deliver on that expectation with quicker turnaround and lower cost.’
Jakob Landberg, global sales director at Nilpeter, commented: ‘All our presses are manufactured to the highest accuracy in-house. The frames are welded together and powder coated, with all drilling, grinding, and threading processes completed in one step. In this way, when our customers store positions in the job files, jobs can be recalled to the tightest tolerance with the presses holding ultra-tight register over the run length, and consistency from job to job.’
TQL’s FA-26 is equipped to cure UV and E-Beam lamination adhesives to produce a wide variety of flexible packaging. E-Beam lamination has proven film-bonding properties with multiple substrates, including BOPP, PET, and LDPE based sealant films, aluminum foil, and papers. EB laminated structures exhibit good water and food resistance, are suitable for food packaging with FDA compliance and are odorless.
‘Nilpeter’s ability to integrate E-Beam lamination into the press, achieving the smooth level of communication required to meet the quality and speed we need to service our customers, has been impressive. The market for what the machine can do is so much greater than what we estimated. Between new work and cutting in on traditional gravure business, the future looks bright for our business, and I expect we’ll need a second FA-26 very soon,’ concluded Smith.
Stay up to date
Subscribe to the free Label News newsletter and receive the latest content every week. We'll never share your email address.