Vac Pac invests in Soma Optima2 flexo press
Baltimore metro-based Vac Pac has invested in an 8-color 59in Soma Optima2 flexo press and an automated Soma S-Mount plate mounter.
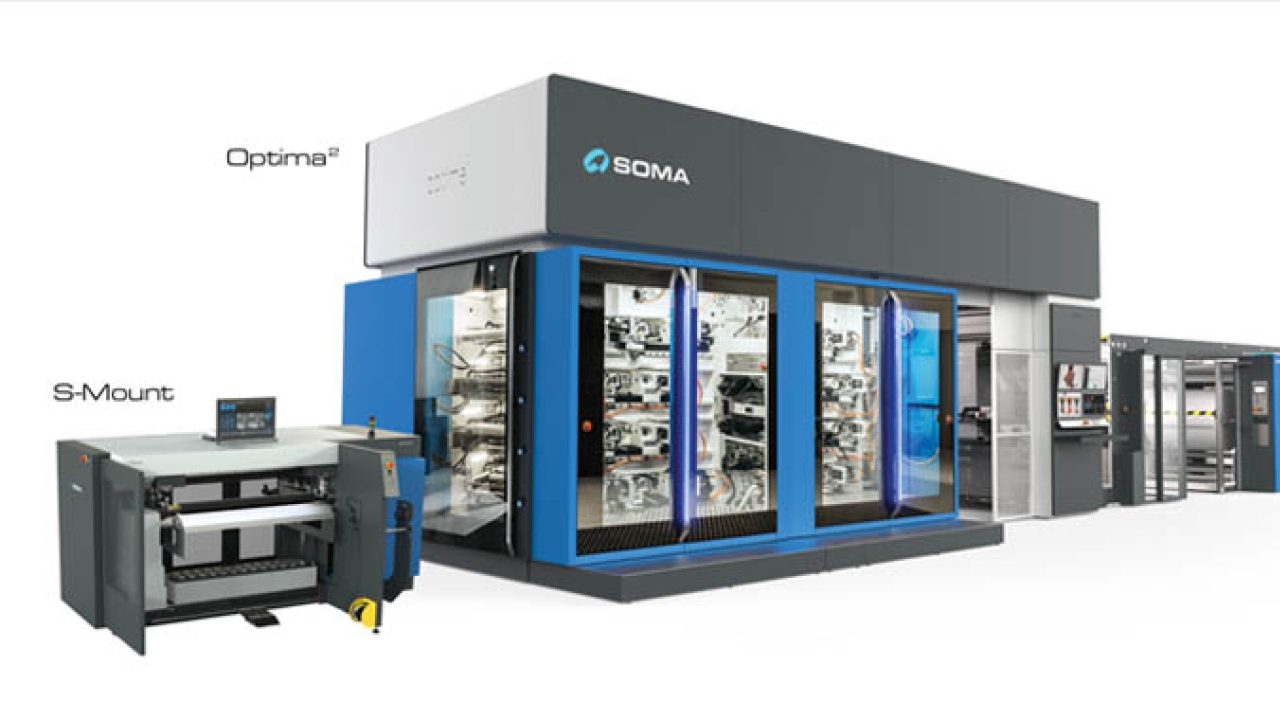
Founded in 1928 as Duradene, a maker of cosmetics, today Vac Pac has grown to a multi-generational family business focused on packaging. The company’s 30 employees design, print and manufacture bags and pouches for bakery, poultry, meat, seafood and industrial applications. The company specializes in high-temperature cook-in packaging for oven and microwave cooking as well as high barrier shrink bags.
Vac Pac holds patents for bag design since 1968. It exports finished products around the world through partnerships in South America, Canada, New Zealand, the United Kingdom—and has prospects in other European countries and Asia.
Matt Tary, Vac Pac president, said: ‘In the barrier shrink bag business, there are about five companies that are heavily involved in the market. Three of our competitors are billion dollar businesses. It means that Vac Pac has to work harder to execute a successful business plan and earn our customers’ respect.’
Vac Pac currently owns two flexo presses, a 6-color and a 10-color. It is replacing the existing 6-color press with the Soma Optima2. As a smaller company, it needed to modernize and push the boundaries of its work to get new business. The new Soma press will enable it to do so.
‘Our company is very different from most small converters. Many of them specialize in only one type of work. We get involved in a number of very specialized niches, changing materials very often from job to job, from shrink tubing to poly sheeting to PET materials for oven roasting. We looked for equipment that is versatile. The Soma Optima2 was the first flexo press with real potential to offer flexibility and execute well across all our demands. For example, while we produce very good print quality work, our limitation has been that we currently print on only one side. Soma can provide its Optima2 press with a turn bar, which will allow us to print both the front and back in one pass, in register. We will now be able to be significantly more aggressive in the market with this two side capability that our customers are looking for,’ Tary explained.
Vac Pac was impressed with Soma’s fast speeds and quick changeovers. The company was interested in faster changeovers and reducing scrap.
‘Tube material is expensive. With the use of the automatic Soma S-Mount mounter, there will be very little waste in the setup. Reading registration and impression settings automatically into the press will save a lot of time. The Changeover Wizard is also very intriguing. We have the same problem as everyone—hiring skilled flexo printers. To be able to take untrained people and quickly put them into operation, is the future,’ Tary added.
Vac Pac and Soma are both family owned and operated. ‘Thus, as the grandson of the person who moved Vac Pac into packaging, I felt connected with Pavla and Jan, whose father founded Soma. We have already been very impressed with our tech consults and have been very comfortable with the purchase experience. The Czech mentality is to build their equipment like a tank, but with intelligence. We’re learning that,’ Tary said.
The Soma Optima2 is said to be three times faster than Vac Pac’s existing presses.
Stay up to date
Subscribe to the free Label News newsletter and receive the latest content every week. We'll never share your email address.