Cromograf’s path to sustainable packaging recognized with innovation award
Uruguayan pre-press specialist receives Gold Award in the Miraclon Global Flexo Innovation Awards
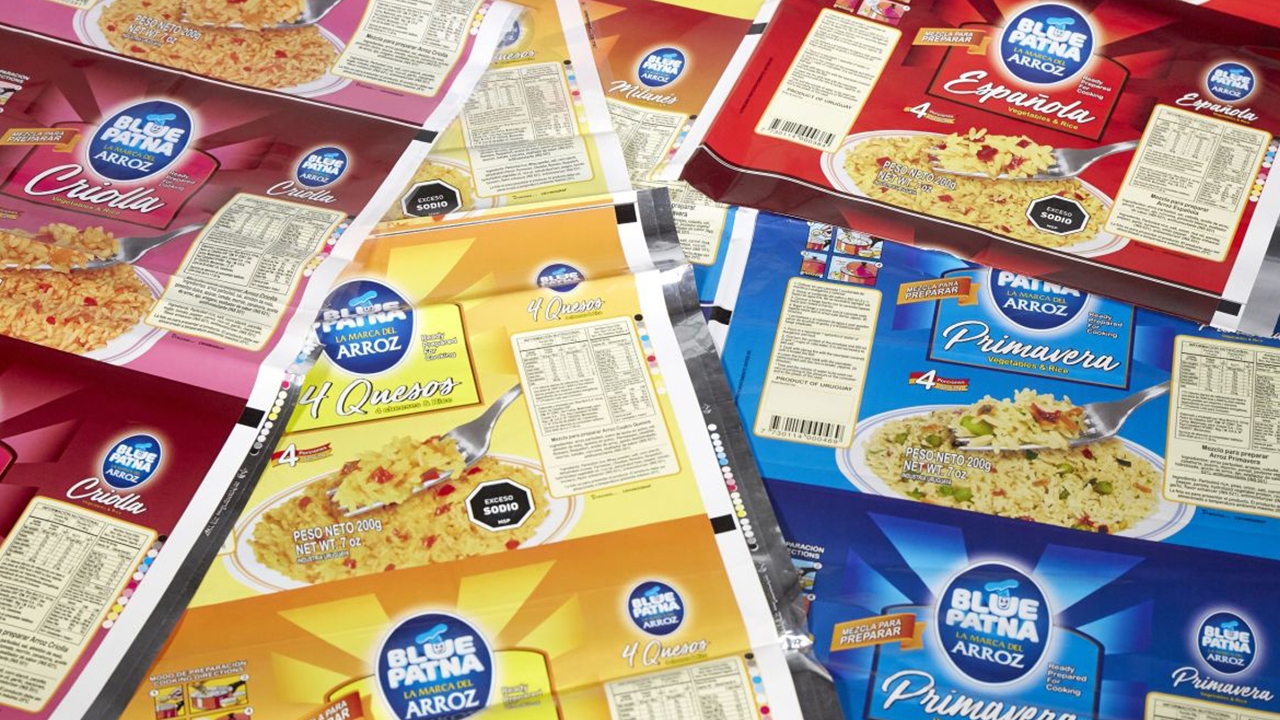
Cromograf has been recently recognized with a Gold Award in the Miraclon-sponsored Global Flexo Innovation Awards
Over the last decade and a half, Uruguayan flexo packaging prepress trade shop Cromograf has reached beyond its Montevideo base. The company has been recently recognized with a Gold Award in the Miraclon-sponsored Global Flexo Innovation Awards (GFIA) for excellence in Print Production Workflow, Commitment to Sustainable Print, and Creative Use of Graphic Design.
CEO Alejandra Acosta Salati puts the success down to what she describes as the company’s ‘restless DNA, which is always motivating us to improve. As a result, we have become something of a laboratory of innovation that has driven change in other trade shops.’
Cromograf’s embrace of sustainable production is a good example of the company’s pioneering spirit. While the thoughtful, planned use of resources may now be a mantra for all stakeholders in the packaging supply chain, Cromograf already embarked on the path in 2008.
‘In a way, it started the day my father, Miguel Angel Acosta, saw the Flexcel NX system. He immediately recognized the potential of a technology that eliminated variables and brought new levels of consistency to the flexo process,’ said Salati. ‘We believe in streamlining and standardizing processes as much as possible, and the Flexcel NX system provided the best platform for standardized, repeatable production. That’s the way it was then, and it’s the same now.’
Cromograf installed the first system in Latin America in 2008, and a few months later began experimenting with Extended Color Gamut (ECG) printing; a process in which – 14 years later – Cromograf is recognized as the technology leader in Latin America and beyond.
ECG is the foundation of Cromograf’s sustainability policy, because of the savings and efficiencies that are inherent in the basic idea of printing as much as possible using a fixed CMYK ink set.
‘ECG uses fewer plates, fewer special inks, and cuts substrate wastage during job set-up. In addition, and this is very important for brand owners, the standard ink set means we can print multiple jobs simultaneously,’ commented Salati. ‘This makes it easier to meet converters’ minimum order quantities despite ordering smaller volumes, which helps with test-marketing of new packaging ideas.
‘The whole concept of ECG is to remove variables that can impact productivity and reduce sustainability. FLEXCEL NX Technology allows for standardized production to achieve predictable, consistent results. It’s an exceptional plate technology that offers high productivity and process stability. The dot reproduction remains stable print after print, giving us consistency, longer plate life and fewer unscheduled press stops for cleaning.’
For the company, the Global Flexo Innovation Award is a welcome recognition of the strategy started by her father and continued under her management.
‘We have been printing with CMYK and ECG since 2008 and take pride in the quality of what we produce. The difference today is that people are taking notice,’ said Salati.
The GFIA judges were also impressed by how Cromograf approach each new packaging project in order to decide how best to apply ECG.
Dr Chip Tonkin, from the Sonoco Institute of Packaging Design and Graphics, said: ‘They do a lot of analysis on an incoming job to determine if it needs anything beyond CMYK, and they take extreme measures to do it within CMYK for the vast majority of jobs. For most colors, you can achieve it with CMYK, particularly when you optimize your CMYK.’
‘The packaging value chain begins with an idea and ends when the packaging is in the hands of the consumer. Along the way, we consider the use of every resource input, controlling the process at every stage with the goal of producing a stable product with a minimal carbon footprint,’ concluded Salati.
Stay up to date
Subscribe to the free Label News newsletter and receive the latest content every week. We'll never share your email address.