Automation and artificial intelligence
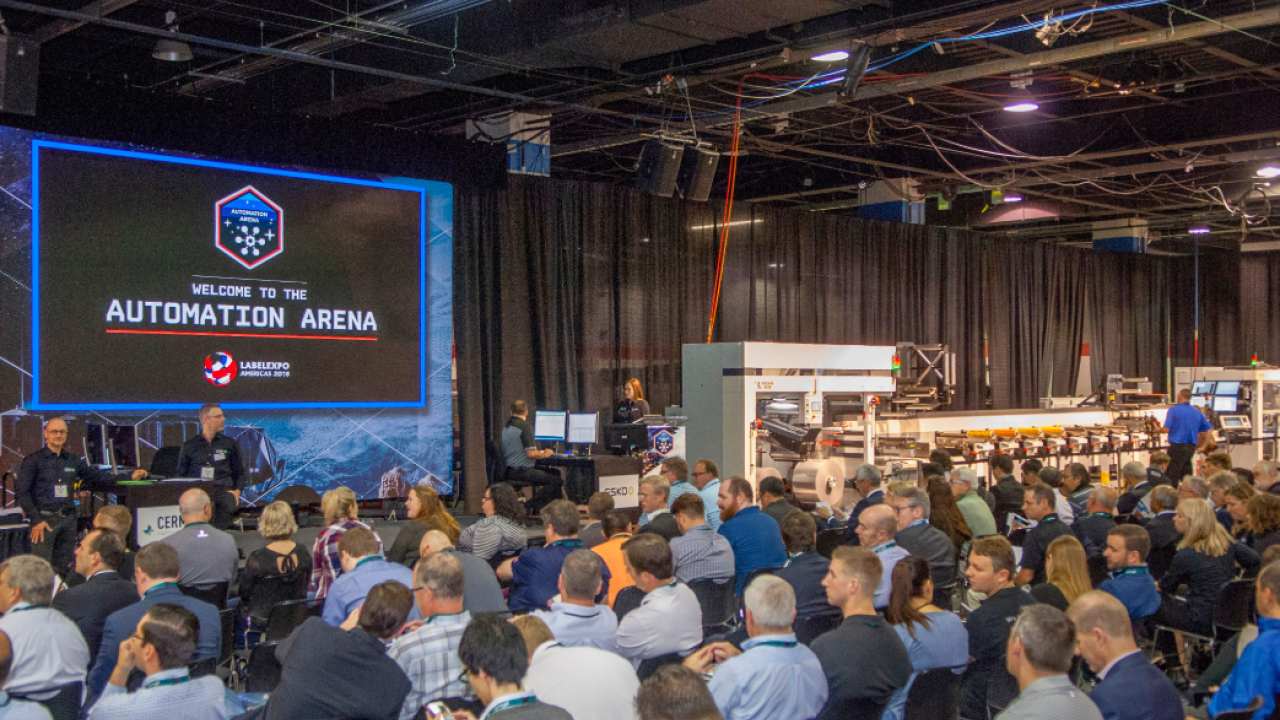
Whether it is the use of smart phones, smart meters, automated payment systems, travel ticketing, navigation, search engines, online assistants (Alexa and Siri), self-driving cars or lawnmowers, smart lighting, social media apps or just ordering an Uber, all are impacted to some degree by artificial or machine intelligence, automated processes and smart technology
The label and packaging industries are not immune to such advances. Each year sees new evidence of how artificial (machine) intelligence and automation of workflows, processes and systems is changing the way the industry performs, improving efficiencies, reducing lead times and wastage, enhancing quality inspection, and better serving its brand, retail and other customers.
Visitors to Labelexpo Europe 2017 and Labelexpo Americas 2018 cannot fail to have seen how many booths were showing equipment or systems for automating various press operations, unwinding, slitting and rewinding machines and other types of finishing or end operation equipment, the pre-press processes and proofing operations, or workflow automation managed by increasingly sophisticated MIS.
High level of interest in Automation Arena
Indeed, such is the interest by the industry in what is taking place, that over the last two Labelexpo shows some 2,500 visitors have attended the Automation Arena demonstrations of the automated label, shrink sleeve and package printing plants of tomorrow – with a level of automation, machine intelligence, performance and profitability never before attempted.
The overall aim of the Automation Arenas has been to show converters that with the latest integrated workflow technology and machine intelligence it is now easier than ever to automate and process many more jobs in the same throughput time, with fewer errors, with 100 percent quality and barcode inspection, incorporate automated press and finishing set-up, and all with the same number of employees.
At the most recent Labelexpo Americas show there was a unique collaboration between 14 key label industry suppliers, with a Cerm Management Information System (MIS ) as the central hub. A global provider of business management and automated software for both traditional and digital label narrow web converters, Cerm teamed with international industry partners to develop end-to-end automation solutions for self-adhesive labels and shrink sleeves that now cover the entire value chain.
During the automation demonstrations, the Cerm MIS was seen processing and managing the whole automated workflow, integrating with an Esko Software Platform supporting end-to-end label workflow. This platform firstly changed the selected digital label design being produced on Avery Dennison self-adhesive labelstock printed on a Xeikon LDU digital press – and personalized the artwork with the customer’s name, created rules for inspection, and initiated a proof for customer approval – followed by calling-up the shrink sleeve graphics and plates for printing on an MPS EF-APC UV flexo press.
The Esko Software Platform 18 being demonstrated provided a comprehensive set of software solutions for design and pre-press, workflow automation, color management, and supply chain collaboration. With a focus on cost control and productivity optimization, the platform supported an end-to-end workflow with hyper realistic 3D viewing, also on mobile devices, web collaboration, PDF editing, content management, and quality assurance tools all providing a sophisticated user experience.
Digital printing, laser cutting and inspection line
Once approval of the label and barcode was received back from an audience selected ‘customer,’ files were sent from the Esko Software Platform to a Xeikon X-800 digital front end, in turn integrated with a Xeikon LDU laser die-cutting unit that was able to ‘needlessly’ switch over between two jobs.
The Xeikon LDU applied a Flint Group Digicoat GP gloss varnish, laser die-cut, slit and rewound the labels, enabling frequent job changeovers with limited or no set-up time. Integration with the Xeikon Front-End via the Vectorizer module provided step and repeat and printing, with AVT 100 percent automation inspection files, job identification and die-cutting, and finishing barcodes for the in-line laser die-cutting, slitting and turret rewinding. The finished rolls off the press were barcoded for roll identification of the finished product.
A Matho Cuttobag CB-100.1 waste management system on the Xeikon press was used to cut, transport and collect the production waste into a waste disposal system, while cores for both presses were being cut on a WLE fully automatic core cutter. The cutter read a barcode from a label printed on a label printer close to the cutter. This requested job cutting instructions from the MIS, while the label was reused to identify the cores per job.
Non-stop UV flexo sleeve printing
With the Xeikon press set-up and running, the MPS EF-APC operator was already reading his MIS-generated job ticket on screen, enabling him to check that plates, tools, inks and substrate had been delivered, and changing the unwind roll using a Kocher + Beck UR Precision U440 butt splicer. This highly innovative technology featured a fully servo-driven unit with intelligent Data Link communication features, providing non-stop press operation and increased throughput. Because it was a reprint, the MIS provided the press with the appropriate set-up file stored, avoiding any search time lost by the operator.
Each roll loaded was scanned and became fully traceable throughout the whole process, interacting with the Cerm system in order to provide real-time production values. A Cerm inspection command was also sent to AVT’s automatic 100 percent print inspection system for detection of spots, streaks and color on each print deck – providing fully connective technology ready for Industry 4.0 implementation – which registered any defects during printing, but at this stage did not act on them.
Especially designed for labels, sleeves and flexible packaging production, the MPS EF-APC press operated with no gear cylinder connection, intelligent pressuresetting and zero waste roll change, and featured UV, hot-air and LED drying technology, enabling users to print on a wide variety of substrates, including thin film, paper, carton board, shrink sleeves, in-mold, tubes and flexible packaging. It printed on a Klockner Pentalabel shrink film using Zeller + Gmelin’s 32 Series Nuvaflex range of UV flexo inks developed specifically for sleeve production.
Next to ‘standard integrated’ machine automation, the EF-APC also offers an automation package for further extended (additional) print automation: the APC Package provides automated servo control of all relevant press settings. The package can be configured for the ultimate in print setting control to further increase productivity on the EF press. Automation extends to sleeve seaming and finishing.
Automation extended to sleeve seaming and finishing
Printed rolls coming off the MPS press were identified with an ID barcode generated by the MIS which, when scanned, enabled an electronic instruction file to automatically set-up shear slitting on a Grafotronic H12 high-speed inspection slitter rewinder, as well as providing the location for any bad products according to AVT scanning instructions.
An AVT camera on the Grafotronic automatically stopped the machine whenever a defective label was detected in the printed reel so that any necessary repairs could take place. The final, ‘clean’ and slit roll was then rewound and a barcoded label applied to the reel. As this roll transferred to an AccraSeam FC fully continuous shrink sleeve forming and seaming machine, equipped with a fully-automatic table with seam positioning, the barcode was scanned and the instruction file from the code read and used to automatically set-up the forming and seaming operation.
After set-up, forming, seaming and rewinding of the, now, lay-flat shrink sleeve web, the Accraply ASFC wrote a log file and created a barcoded label which was applied to the lay-flat seamed roll coming from the seamer. This barcode was, in turn, then used to identify and provide file information as the seamed roll was transferred to an Accraply DM12 Shrink Sleeve Inspector, a compact vertical seaming inspection machine used for lay-flat quality checking.
The DM12 inspected for seam integrity, solvent presence, lay flat and for any splicing/flag detections, enabling any bad sleeves to be thrown out before rewinding the lay-flat ‘clean’ web. At the end of the quality check the Accraply system provided a printed report for each roll that gives the customer all the necessary QC information required.
Final rolls carrying barcoded identity information, whether from the Xeikon or the MPS/Accraply production lines, were scanned into a warehouse location, a picking list prepared through the Cerm MIS, a delivery note printed, and e-mail notification sent to the customer and invoicing launched. All of the production data is permanently collected by the MIS and presented in a Smart Business Intelligence system, whether it is about sales, production or profitability.
Ongoing automation developments
While the Automation Arena demonstrations provided an exciting glimpse into tomorrow’s automated label plant, other Labelexpo exhibitors were also busily taking further automation steps. Ink logistics provider GSE, for example, showed enhanced ink management software that enables converters to minimize ink-related waste, providing improved ink yields, enhanced reporting and reduced set-up times.
Color management workflow technology from Baldwin also now automates the process of delivering absolute consistency from pressto-press, shift-to-shift, and plant-to-plant. Reporting tools enable quality managers to deliver full production overviews to print buyers and brand owners.
Another interesting development has been the acquisition of Blue Software by Esko. This is targeted at further reducing time-tomarket, cost and quality risk in the end-to-end label and packaging chain. Software and hardware systems now digitalize, automate and connect the whole label and packaging and development chain, from virtual 3D design concept all the way to printed, finished and labeled packs and in store displays.
Put together the Automation Arenas, Label Academy ‘MIS and workflow automation’ text book and Master Classes, plus new industry vendor advances, are rapidly taking the industry into a new level of machine intelligence and automation that offers the possibility of providing new and unprecedented levels of service to brand owners, retailers and other customers.
What is now in sight is the ability to take a brand owners materials specifications, label or pack compliance, BRC, ISO and QC requirements, sustainability demands, etc, and bring them all into one automated label production and workflow system that will automatically print and then generate all the necessary compliance or sustainability certification documents to be automatically sent to the customer when the job is shipped.
Such certification might include materials FSC or recyclability, color match and color consistency, printability tests undertaken, UV ink cure, materials run, ink and substrate wastage, percentage waste sent for recycling, exact finished label count, 100 percent label inspection, and much more.
A need for standards and protocols
However, to get to this stage, more industry vendors will undoubtedly need to be brought into the automation process. There also seems to be a need for a more specific common label industry JDF/JMF language, standards and protocols; a requirement for ‘interoperability conformance specification’ with ‘best practices’ between the two parts of the workflow (eg between MIS and pre-press); and maybe a certification process to guarantee the level of the solution supplier (and not having to discuss every time).
Why is this needed? Well, at the moment, not all label industry vendors are CIP4 members and/or do not use a JDF standard. Maybe the label and package printing industry suppliers need to establish their own JDF forum or workgroup to discuss the pros and cons of JMF as it specifically relates to the label and package print sectors, review the new XJDF proposals and how they relate to the industry, and see if they need to be even more simplified, modified or to become more complete.
Yes, there is a standard already for the graphical industry, but if more label and package printing materials, equipment and systems suppliers were to become involved in study and work groups, then the industry can become even more creative in the future.
Stay up to date
Subscribe to the free Label News newsletter and receive the latest content every week. We'll never share your email address.