Screening software key to inkjet productivity
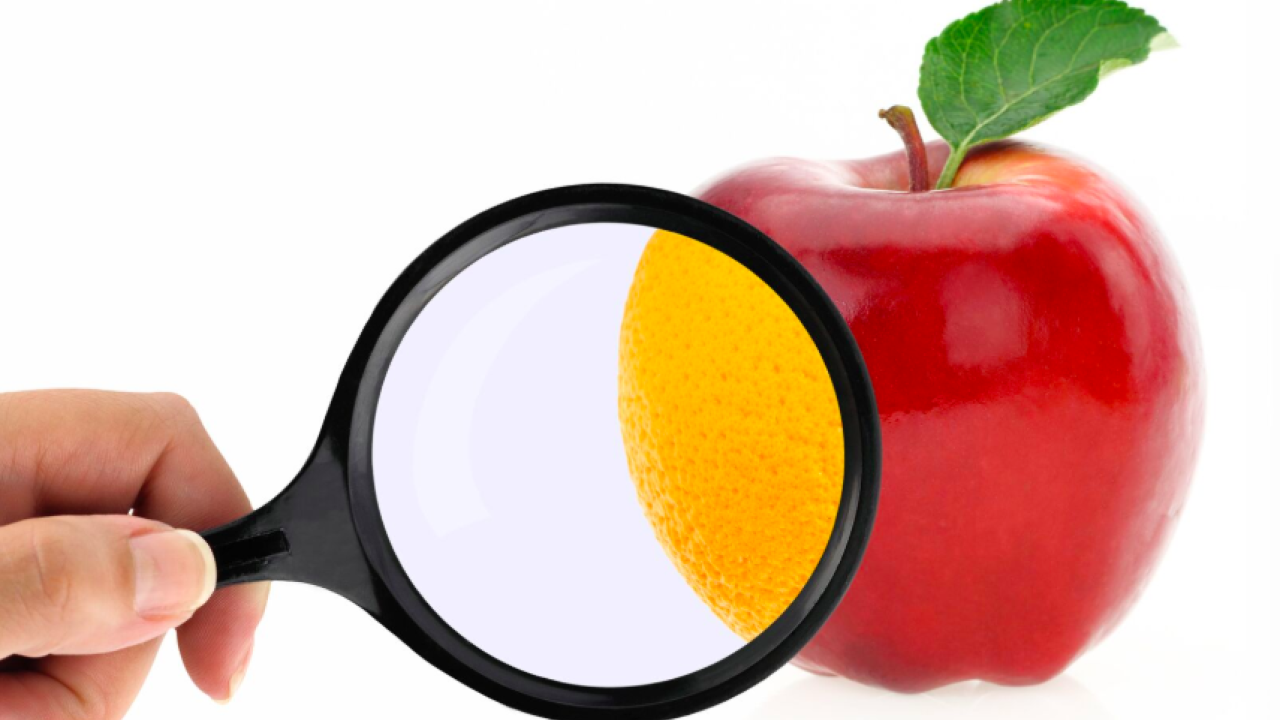
The productivity benefits are clear. But if you look at the figures quoted by Mark Andy for its Digital Series press you’ll have noted that they achieved 50 percent more RIPping speed by being able to screen variable images at speed directly on the press.
While inkjet technology is moving quickly, the choice of screening software can make a huge difference to the productivity of your digital printing operation.
Areas in which inkjet presses can disappoint include the readability of small text and barcodes, the appearance of flesh tones and highlights, and the uniformity of areas of flat tint. Through the work we do with our OEM customers, we hear that many jobs cannot be printed with confidence on inkjet presses due to directional variations – streaking or banding – that are obvious at the desired viewing distance.
So when I wander around tradeshows and hear claims that inkjet has finally attained the same quality as offset or flexo, I’m slightly sceptical.
Inkjet pros and cons Inkjet is different from a conventional press and has distinctive strengths and weaknesses. If you’re examining the detail in photographic images then modern inkjet will score very well, at least partly because most vendors usually use some form of dispersed screening (stochastic or FM), which can reproduce far more detail for the imaging resolution than a clustered or AM screen can. And when you add in greyscale heads that can place differing amounts of colorant in each location on the substrate, it gets even better.
Now look at small text. Inkjet will often be printing at a lower resolution than offset, and much lower than high-quality flexo, and that has an impact on how well fine vector graphics can be reproduced. The ink technology used, in combination with how that ink reacts with the substrate, also affects this area. Detail such as serifs in small text will often look heavier (on UV or aqueous on coated stocks) or may even disappear completely (using aqueous inks on uncoated stocks).
In some sectors, especially those with strong brand oversight or regulatory requirements, text is often converted to outlines in pre-press, rather than using live fonts. But that will tend to make inkjet rendering even worse in comparison with conventional presses and increases the likelihood of very fine detail such as fine horizontal or vertical strokes disappearing completely, unless you’re using a solution that’s specifically tuned for common digital press resolutions.
Overcoming non-uniformity
Another area in which inkjet has more challenges than offset or flexo is in printing relatively large and flat regions of mid-tone tints. That’s because inkjet has a tendency towards several different classes of non-uniformity in the output, which are typically split into microscopic and macroscopic: small and large artifacts.
Microscopic variations are often described as streaking, graininess, noise or mottling, and can occur for several reasons: drops coalescing on the surface; heads being misaligned; ejection timing not being quite right; drops being disturbed by eddies in the air flow between the heads and the substrate; ink shrinkage during drying or curing.
Macroscopic variations are the banding that you get along a single pass printer or across a multi-pass or scanning printer. The unevenness is caused by variations both within and between inkjet heads along the print bars in the press. This can be caused by: ink pressure and voltage changes across the head; differences in manufacturing; certain types of head/ink combinations wear with use. The more drops emitted, the more the head wears.
These issues can be caused in many different ways, and most inkjet presses suffer from at least some of them to varying degrees. Where do you start to overcome them?
If you’re a press vendor and your product suffers from microscopic artifacts, the first step is obviously to review your inkjet press design, for example considering ink formulation with respect to the substrates to be used and all the mechanical adjustments that can be made such as throw distance, waveforms, air-flow, and substrate movement.
But at some point, any improvements to the physical design start becoming more and more expensive, and improvements to ink formulation begin to counteract other requirements, such as the need for open-time, drying or curing efficiency. It’s often not possible to engineer all microscopic artifacts out of the system at a hardware, ink and electronics level. Yes, you could do more trouble-shooting but it’s just going to cost too much up front. It’s going to delay your time to market and make the press too expensive to build.
The good news is that microscopic artifacts are often amenable to correction in software by using a specifically designed halftone screen. Something that counteracts the directionality of the inkjet system, which is what leads to drop coalescence and therefore to streaking. Or that manages the ink shrinkage during curing and drying that leads to mottling and graininess.
If your output suffers from visible banding or macroscopic nonuniformity, that is simply due to variations between and within inkjet heads, or between swathes on a multi-pass press. Pretty much every inkjet printhead design has this issue to at least some extent, and historically press vendors have countered it by careful selection of which heads will be used, combined with adjustment of voltages for each head, or for each region of each head.
Those techniques certainly improve matters but tend to make it slower and more expensive to build each new press and complicate on-site maintenance, especially if heads must be replaced on an existing press in the field, which can result in downtime for the converter or print shop.
The most cost-effective and efficient solution can be applied in software. For example, our PrintFlat technology adjusts halftones for every individual nozzle as they are applied to compensate for the tonal changes that will occur when the output is jetted onto the substrate.
The need for speed and quality
Another aspect of the complex interaction between components in an inkjet workflow and press is that the solution for non-uniformity must be fast enough so that the press can run at full speed, even when variable data is involved and every print is different.
Take, for example, the Mark Andy Digital Series HD, which made its debut at Labelexpo Americas 2018 and which prints pressure-sensitive labels at 240 linear ft/min (74m/min). The press supports 4-6 digital color formats in a hybrid digital and flexo press configuration and offers unlimited color variable data options at full speed. It uses digital inkjet print heads supporting multiple drop sizes. Because each label can be different and at variable places on the web, it becomes more difficult to maintain a queue of VDP jobs. Text color and imaging needed to meet customer requirements. As the Digital Series press was being developed, Mark Andy quickly realized that a highly capable RIP, hardware and software suite were required to process VDP jobs sufficiently fast to avoid press shut downs due to a lack of RIPped VDP work loaded on the digital press job queue.
We developed a version of our multi-level screening engine ScreenPro, called ScreenPro Direct, which is an online component that drives the press directly and screens as it prints. It maximizes image print quality for high-speed production inkjet printing, with no loss in performance even with additional print bars to support extended gamut colors. There’s no limit to the number of VDP elements on one imposition, meaning every page is different.
So, does that mean that inkjet has achieved offset quality?
Clearly, high-speed, fully variable, full color with high image acuity on inkjet is possible with the right choice of screening software and the right kinds of graphics, such as photographic images with lots of detail. Global Graphics Software’s technologies are helping vendors to get very close even on challenging graphics such as flat tints and long gradations.
We’ve also been working on related topics, including specific algorithms for maximizing the quality of small outlined text at inkjet resolutions in our Harlequin RIP.
Stay up to date
Subscribe to the free Label News newsletter and receive the latest content every week. We'll never share your email address.