Driving efficiency by reducing waste
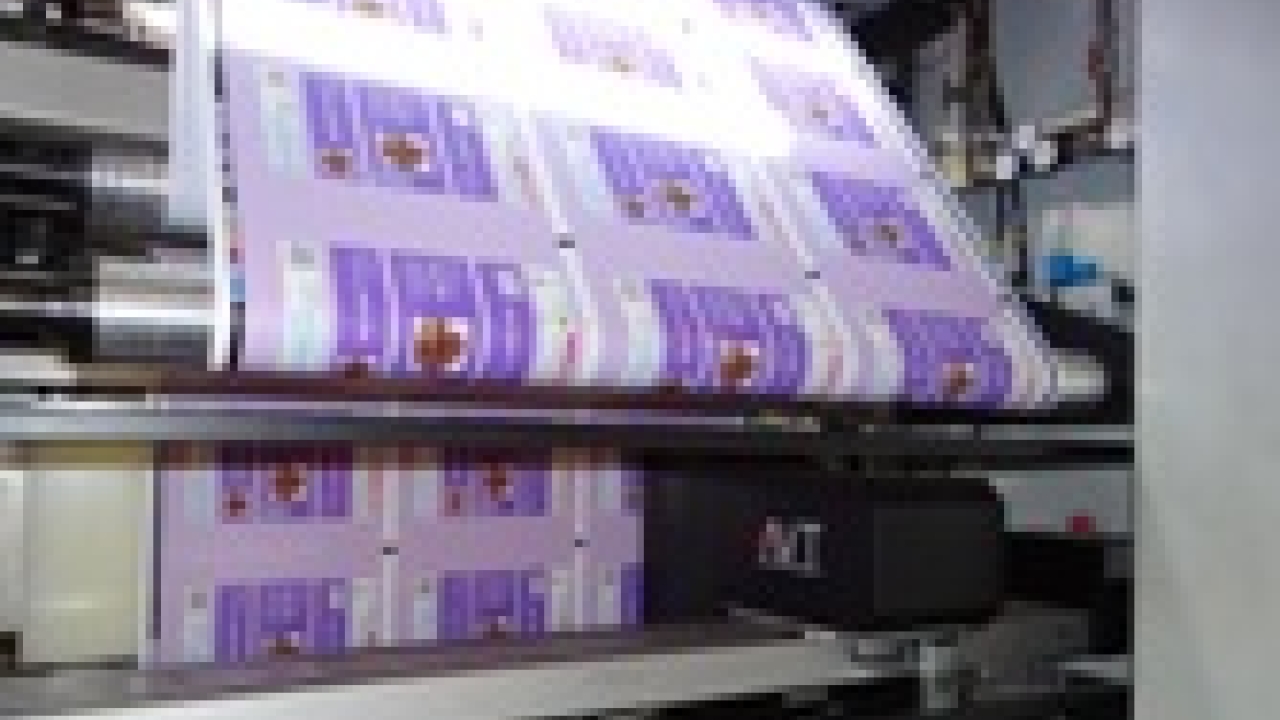
How to improve the production speed of your CI flexo press was the problem facing long-time industry professional, Harvey Ball, when he took over the running of Reflex Flexible Packaging in April 2010. Nick Coombes reports
Reflex Flexible Packaging is an independent company with six manufacturing sites across the UK. Formed in 2002, the company lists flexible packaging, design, artwork, plates and variable data printing amongst its services. In addition, the entire Reflex Group is BRC certified and the Newcastle site is an FSC and PEFC certified supplier.
Reflex Flexible Packaging’s plant in Telford, UK manufactures high-quality food packaging on substrates from BOPP to PE, and on substrates from 12 microns upwards, but it was unable to print consistently at speed on its Soma press, in a market where high volumes are the norm and top quality "a given". Ball, who inherited the production technology when he moved to Telford, found a labor force that was disheartened by its apparent inability to make the machinery perform as it was designed to. The solution proved to be simple and came in the form of a print inspection system that monitored the moving web and alerted the operator to any deviation from a master image. The system chosen was the PrintVision Jupiter, manufactured by Israel’s Advanced Vision Technology (AVT).
‘I cannot understand why anyone would buy a modern high speed press without an inspection system – I liken it to buying a high-performance car without a steering wheel,’ says Ball. ‘It’s uncontrollable.’
Narrowing down his choice of supplier to what he perceived the two leading contenders, Ball chose the AVT system after several convincing demonstrations of the technology at leading UK packaging converters. Acknowledging AVT as the pioneer of print inspection systems, he says: ‘If it is the preferred choice of major international package printing groups, I figured it would do a great job for Reflex.’
The AVT system offers advanced print process control for automatic defect detection. It has a unique platform and innovative software that allows Reflex to "catch the problem, before it catches them". By comparing the printed image on the moving web with the approved master copy stored in its computer, the AVT system alerts the operator both visibly (orange light for slight deviation, red for major) and audibly with an alarm, when any problem occurs. The fault is highlighted on the control screen with a series of color-coded marks. These differ for: printed color variation, streaks, mis-registration, spots, or splashes and the computer then stores these marks in a printflow report so that the bad material can be removed from the web downstream
The net result is a massive saving in wasted material and the avoidance of costly reprints. By knowing exactly where in the reel the fault occurred, the laminator or slitter rewinder operator can maximize use of the good print. The system, which is fully automatic, can be set up to different tolerance levels, but otherwise requires no human input or adjustment. Significantly, at Reflex, the AVT system also includes the optional pRegister module. Part of this is iReg, which brings the press into register automatically on each new job. Using the existing camera, pRegister automatically fine tunes the press by measuring the mis-register and making adjustments so all the plates are synchronized. Key to the accuracy is a microdot that is laid down at the platemaking stage. The system automatically locates these dots, and sends signals to the CNC motors on the press, which adjust the plates until all colors are perfectly aligned.
According to AVT’s corporate vice president of marketing Amir Dekel: ‘The beauty of iReg is that it takes less than 60 seconds to bring the press into perfect register, even on a 10-colour machine.
The system is accurate to within 15 microns, and as well as reducing make-ready times – at Reflex down from 20 minutes to five – it limits the wasted material on set up to as little as 50m.
Crucially, it also offers a fast payback on investment. Because there is no need to add marks on the trim, existing plates can be used.’
Available as a part of the OEM specification, or as a retrofit, the PrintVision Jupiter system was fitted to the four-year old Soma press at Reflex in between jobs, which avoided any loss of production. Taking less than two hours to install, and requiring no more than 30 minutes operator tuition, the system allows for the camera to be mounted at the most convenient location on the press (ground level and accessible), and once installed, allows the operator to focus attention on running the press, safe in the knowledge that if a print problem is detected, the system will respond automatically. In simple terms, the investment in AVT technology has given Reflex Flexible Packaging a degree of productivity that its workforce could only dream of before. Being able to offer consistent quality to its customers, and allowing them a reduced time to market, has also given the Reflex plant a new lease of life, with fewer reprints, and a much higher level of expectation.
‘I’m confident we made the right choice with AVT. We’ve had few problems since installation last September, and most of those have been of our own making – irrespective, the after-sales support has been top notch. The key fact is that the AVT system has lifted our production speed from 80 to 300m/min, and reduced our waste levels. I estimate it will have paid for itself in less than 12 months; now, that is a good return on investment,’ concludes Harvey Ball.
Stay up to date
Subscribe to the free Label News newsletter and receive the latest content every week. We'll never share your email address.