IST Metz looks back to the future
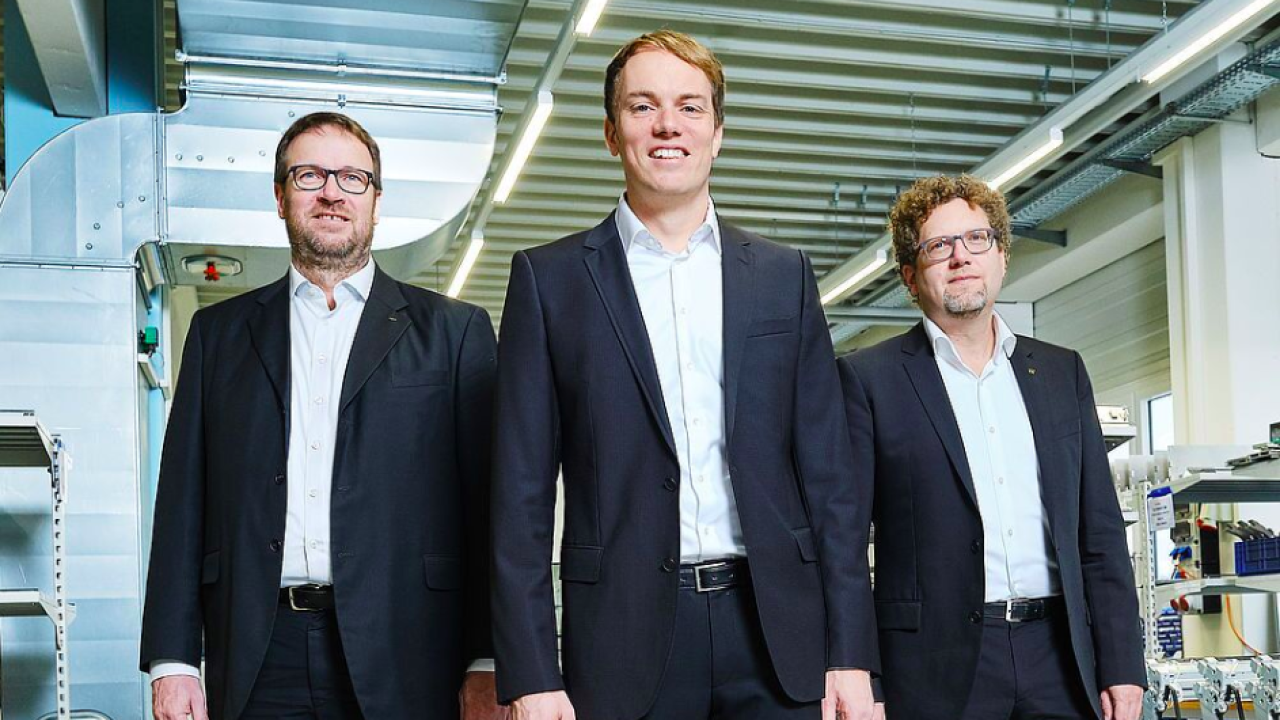
Over the last four decades, this has been exploded to cover multiple graphic arts applications, from conventional narrow web printing and metal decorating to sheet-fed offset and UV inkjet printing, as well as other industrial applications and more niche markets such as water treatment.
Today, the company is seeing its roots re-emerging as an important market for its technologies, alongside label and packaging applications.
Holger Kühn, sales director at IST Metz, identifies how the company’s interests in non-printing applications now account for around a quarter of its business as the company’s markets diversify. This is not an intentional act to move away from printing, rather new applications are opening up for its technologies.
‘The biggest growth we’re seeing is in industrial applications, such as phones, tablets and flat panel displays, and for water purification. The use of our curing technology in these ways and the change in our market mix is a win-win for us. It gives us exposure to both established and emerging markets, which fits well with the theme “Tradition meets modernity”.’
Print in action
Print still accounts for around 75 percent of IST Metz’s business, reckons Kühn. In labels and packaging, advances in specific technologies, namely UV LED, light the way for applications.
This was reported in detail by Labels & Labeling in the aftermath of Labelexpo Americas 2018, while you can anticipate more headlines on UV LED around Labelexpo Europe 2019. It was strongly in evidence again at this year’s UV Days, IST Metz’s biennial meeting for the UV industry, where the likes of Heidelberg, mPrint, Integration Technology, hubergroup, Flint, Siegwerk, Zeller + Gmelin, Evonik and Chromos were featured in a supplier showcase.
To provide physical evidence of UV’s capabilities in all its forms, IST Metz produced a number of print samples. Customized espresso packaging allowed coffee drinkers to choose their beverage based on their personality. Each coffee pack included a treat, wrapped in flexible packaging produced in collaboration with DFTA, the German association for flexographic printing. Lunch was served in SIMPL Dining food packaging produced in accordance with low migration guidelines. Sustainability and individuality were the main focuses of its production. Thanks to the avoidance of plastics and the use of recyclable paper, the box could be unfolded once the food is eaten and disposed of in the paper waste. The UV Days caterer is to continue to use this food packaging after the event.
Sheet-fed printing on a Heidelberg Speedmaster CD 102-7+LX gave attendees a live demonstration of UV and LED curing. Under the theme ‘Tradition meets modernity’, it was producing the PadBook concept that combined traditional office accessories with a modern tablet holder to create a compact mobile workplace. Black was used in the first two printing units, followed by the process colors magenta and yellow. An intermediate dryer was used after the initial application of black and after yellow. A silver spot color was added using the fifth printing unit. In the sixth printing unit, a special effect varnish was applied, creating a fine texture in combination with the gloss varnish. This was followed by another intermediate drying step. In the seventh and final printing unit, PadBook was stamped with a micro-texture. Finally, the gloss varnish was applied via a flexographic unit and dried once more.
A supporting speaker program highlighted how advances in low migration technologies, curing control and de-inking are further moving the UV market forward. Output, lifetime and the cost ratio of LED chips are making that technology increasingly relevant. Pressures coming from up and down the supply chain are also shaping the market.
Challenges
Recent times have seen a shortage in the supply of raw materials, such as the photoinitiators necessary to develop UV inks and coatings. The market for UV curing is then impacted by legislative updates and changes. This is seeing increased pressure through the reclassification of photoinitiators, alongside efforts to minimize the use of mercury. This will provide opportunities for those supplying UV LED technologies as converters look to evolve to meet the demands of their customers – the brands. Kühn sees IST Metz as ideally placed as it offers both lamp-based UV and UV LED curing.
‘We are not trying to force LED, rather we are discussing with our customers what their markets are and what their customers demand. For commercial printers entering UV curing, it is more about how they can evolve and improve their output. With packaging printers, it is a different conversation around economics and flexibility.
‘It will likely mean evaluating their production, retesting for food contact approval, and requalifying all inks and coatings. As such, it is unlikely they will voluntarily make the move unless they have to. Their hands could be forced though as brands and legislators change their rules and require labels to be produced using LED technology. This can result in cost benefits to printers and open them up to new markets.’
In the short term, Kühn does not expect LED to entirely replace mercury curing. ‘It will come, but in the meantime, we offer the Hot Swap system to allow converters to move between conventional UV and LED UV curing.’
The cassette-based Hot Swap system uses one architecture, allowing uses to move easily between IST Metz’s Lampcure and LEDcure systems.
He continues: ‘This gives users the flexibility to move back and forth between the two technologies, improving productivity, especially in the packaging market where mixed-use technology is expected to become the norm.’
Such a system allows customers to adapt to the needs of current and future production techniques. Equipment manufacturers likewise need to have this capability.
‘Well before the advent of Industry 4.0, the industrial revolution saw manufacturing changed by the introduction of steam power and new ways of producing,’ says Kühn. ‘Connected machines and networking will change the future again. Modern systems are sharing ever-more data and talking to each other to maximize uptime. Data is also needed to drive many of today’s megatrends shaping the consumer landscape, such as personalization and digitization. Just look at how we search for information today.
‘However, there is evidence of anti-trends as people look to go on a “digital detox” and take a break from being “always on”.
This can benefit print and the offline world as people look to take time to drink a coffee and enjoy a book, for example, even though technical developments have allowed the modern production of many printed products they’re enjoying.’
With many industries increasingly struggling to strike a balance between continuity of business and faster and faster change, Kühn states: ‘It is important to blend these two aspects and for us to remember that, even as our business transitions into a wider range of applications beyond print, without the past there is no future.’
Stay up to date
Subscribe to the free Label News newsletter and receive the latest content every week. We'll never share your email address.