Rotogravure technology in a changing market
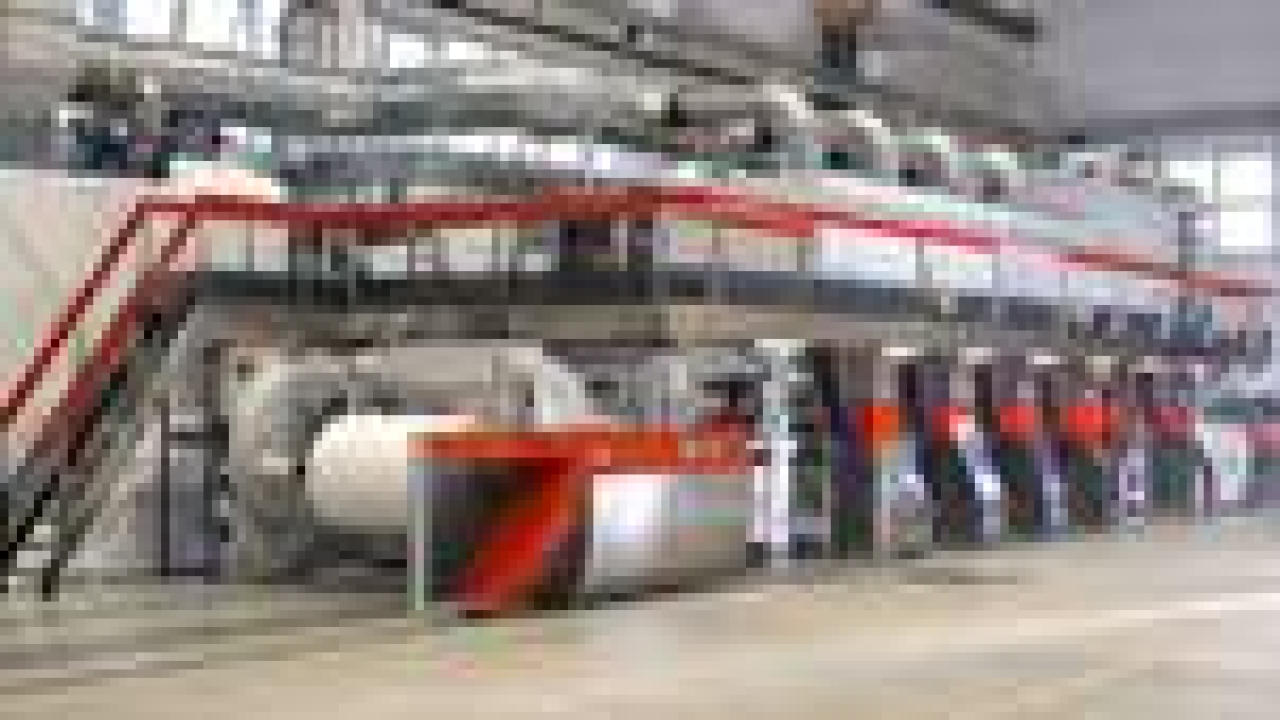
Nick Coombes talks to Costanza Cerutti, communication manager at Cerutti Packaging Equipment SpA, to trace the history of the business, which was founded by her great-grandfather and has grown into a global leader in gravure package printing.
When Giovanni Cerutti started working in his father’s workshop in Casale Monferrato in the late 19th century, he could scarcely have foreseen how the machines he designed and built would go on to gain global prominence more than 100 years later. From such humble beginnings, Cerutti went on to build its first rotogravure press in 1950, which was installed at leading Italian publication printer Mondadori Group.
By the beginning of the 1960s, Giovanni, together with his son Luigi, decided to move into the sector of package printing and established a new plant in Vercelli, which was later expanded to include a purpose-built research and development (R&D) center.
Growing the business
In 1981, Giancarlo Cerutti, grandson of Giovanni, and Costanza’s father, was appointed president and CEO of the Cerutti Group, and the company rapidly became the leader in the rotogravure printing sector, serving both publication and packaging markets. To extend this influence, in 1982 Cerutti decided to expand its presence in the printing communication industry, and installed its first flexographic press for newspaper printing at La Repubblica in 1985. This led to further expansion in Cerutti’s core competences with the acquisition of Flexotecnica, which manufactures CI flexo presses, the Spanish company Iberica, and the American organizations Zerand/ Bernal, which produce various types of die cutting and sheeting machines.
A software design center was opened in 2004 at Trivandrum, in the Kerala region of India, closely followed, in 2007, by Cerutti and Koenig & Bauer (KBA) signing an agreement that transferred to the company all KBA's intellectual property rights relating to rotogravure printing presses for magazines, catalogues and decorative paper. Today, the Italian company is the worldwide leader in this market segment, and holds a majority share in the gravure package printing machine market, employing 930 people around the world.
Technology for modern package printing
The company’s dominance of the package printing sector is the result of its ability to adapt to market trends and invest continually in R&D activities. Within its purpose-built facility, Cerutti has three working presses, complete with a solvent recovery system, and these allow the company to run extensive trials for developing market leading solutions. Costanza Cerutti (pictured, above) explains: ‘It was as a result of monitoring market trends, which indicated ever-decreasing print run lengths, that we developed and launched the Cerutti R970/2 press. It’s a highly automated line, and maximizes productivity by dramatically reducing job changeover times.
‘Our R970/2 customers tell us they now regularly handle 10-20 production jobs in a single 24-hour period.’ This, the company claims, permits its customers to focus on just-in-time orders of high-quality packaging. This new level of productivity applies to both flexible packaging and short-run carton printing.
The R970/2 is a highly effective production tool, capable of printing a large volume of orders each day using machine paced changeover. This system provides the operator with a pre-prepared service trolley for each print unit, complete with a new gravure cylinder and ink tray. At the end of the print run, the machine automatically performs a complete wash-up of each selected unit, including ink tray, gravure cylinder, doctor blade and ink piping. Then, in parallel operation, it automatically changes the gravure cylinders for the new job, and finally, automatically changes the ink pans ready for the new color.
Ms Cerutti says: ‘A full 10-color changeover of all these items, or just the selected ones, can be completed without operator intervention in 12 minutes.
The R970/2 is also equipped with a revolutionary new HC drying system, which increases efficiency by utilizing our own unique circular impinging jets that give a superior heat/mass transfer to conventional slot nozzles.’ The HC dryers, given their unique layout, provide an increased between-unit dryer length, whilst halving the total web length within the press. ‘This also improves set-up waste on each print job,’ she adds.
This automation allows short runs to be profitable, and maximizes the return on investment in a margin-sensitive marketplace. ‘Of course, the machine paced changeover has to be matched by efficient service trolley preparation, but, given the correct preparation, we maintain the R970/2 to be a market leader in short-run gravure printing, and it accounted for 80 percent of our sales in 2010 with a total of 47 presses shipped within the 12 month period.’
Expanding the range
In addition to the R970/2 (pictured, above), Cerutti has further developed its standard cart-type press, the R980, into a series capable of short and medium runs for differing marketplaces. The Cerutti R981/R982/R983 presses all feature a removable trolley that carries the new gravure cylinder, ink tray, ink tank and detachable ink pump, which allows for rapid manual job changeover using a “pit-stop” technique. To cope with extremely short runs, where the next print job trolleys need to be pre-prepared and ready in time, the R982 has been developed and designed in cooperation with washing machine manufacturers, which sees the entire trolley, along with all components, Teflon coated and solvent-resistant, to enable them to be washed and assembled off-line.
‘The R981 is the basic configuration,’ explains Costanza Cerutti. ‘It’s a flexible press for the most diverse of markets, and can use different inking systems with an inner and outer pan, or with inner and outer pans plus idle inking roller. It is also available with integral printing cylinders and with sleeves that are locked by air chucks.’
The R983 is designed specifically for cartonboard printing, and for hologram application or cigarette boxes. ‘This can withstand the very high web tensions needed to run these substrates,’ she says. For short-run markets with a narrower web width, Cerutti has developed the R990. This sleeved press encompasses a special cantilevered change device that allows sleeves to be changed in a matter of seconds, which is particularly useful when no ink change is required.
‘All of our press platforms have been enhanced for further waste reduction using the Cerutti Auto Presetting System (CAPS), which offers customers waste reduction at the start of new and repeat jobs, and has reduced pre-setting times and costs too. An additional register scanning head on the first print unit assists in phasing all the cylinders and sequencing them into register, with a dramatic reduction in material waste,’ she says.
In 2011, Cerutti launched its R1060 format press, designed for specialist applications. It incorporates the automated trolley exchange for reduced changeover times and can be supplied in print widths up to 1,800 mm and with print speeds of 600m/min. ‘The launch went well, and we received many enquiries for applications in flexible packaging, transfer printing and heavy-duty PVC printing for swimming pool liners. It just highlights the Cerutti Group’s flexible capacity,’ she concludes.
An eye on the future
With packaging now such a large part of the Group’s business, Cerutti has established Cerutti Packaging Equipment SpA as a wholly owned subsidiary of parent Officine Meccaniche Giovanni Cerutti Spa.
While many industry experts forecast the demise of gravure printing on cost grounds, Cerutti believes that with skillful R&D, and diversification into new market areas, it has more than enough ability to sustain and grow its business in the 21st century.
Stay up to date
Subscribe to the free Label News newsletter and receive the latest content every week. We'll never share your email address.