Taking digital finishing to the next level
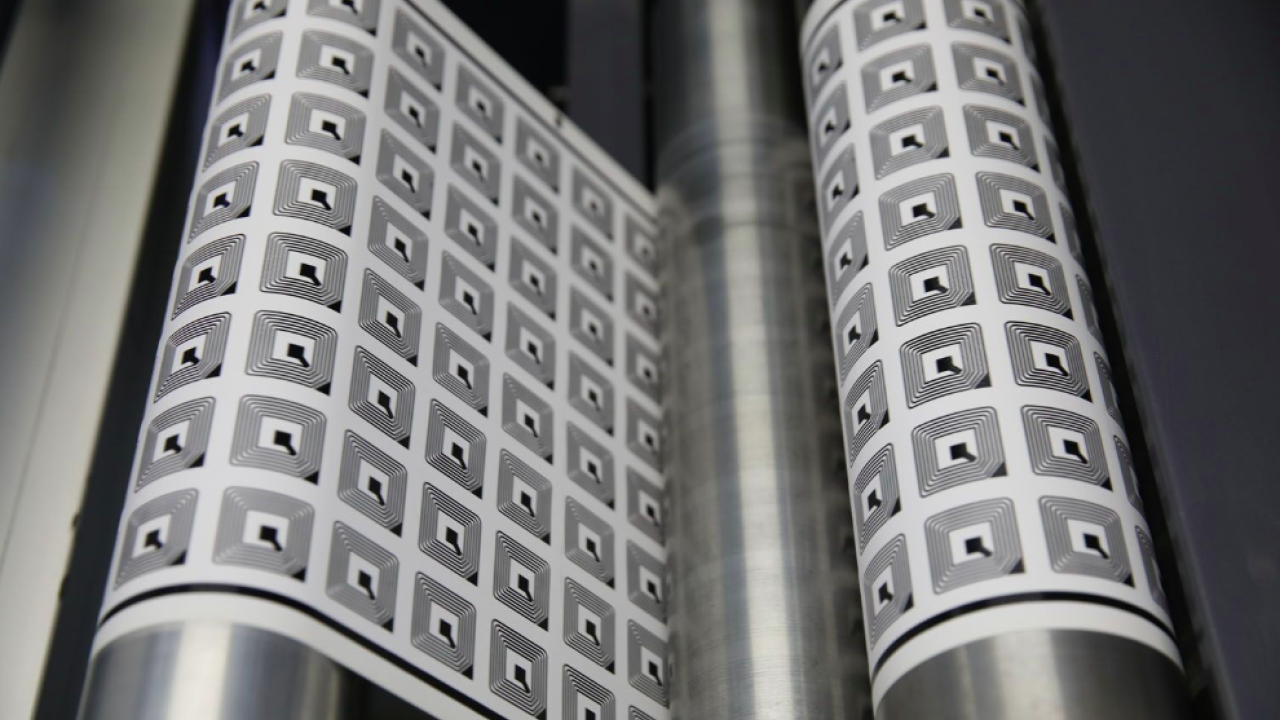
In the design and origination phase, creating artwork specific to the characteristics of toner or inkjet, for example, ensures optimum output can be achieved on-press. Correct material specification and selection ensures suitability for the print process and that the finished product is fit for the application. Finishing ‘completes the cycle of production for a sellable label,’ opines Jason Schmitt, regional sales manager for the eastern US at Rotocontrol. ‘If not done correctly to spec, the resources expended at the printing process can be totally lost.’
Matthias Marx, head of marketing at Gallus, says: ‘A state-of-the-art digital label printing line has to fulfill the same requirements in finishing equipment as a conventional label press, like high print quality and flexibility. New is that the benefits of digital printing, like short run flexibility or variable data printing, have to be added to on top. Label printers and converters need short run flexibility especially for job orders with serialization and individualization as well as industrial data printing for meeting their customers’ demands.’
Morten Toksværd, global sales and marketing director at GM, adds: ‘The printing houses providing digital printing receive many orders for small series of labels. Their clients also expect fast delivery and of course high quality of the products. For this reason, they are looking for smart finishing equipment that may run short and ultra-short jobs without wasting a lot of substrate and the set-up of the machines is reduced to the minimum.’
For GM, this means the key capabilities of digital finishing equipment hinge on automation, efficiency, and embellishments and special effects.
Matt Burton, sales director at AB Graphic, sees diversification as important as adding value and driving efficiency, often through automation. ‘In our opinion, customers are looking for a combination of these three things. To improve their efficiency to provide more capacity and reduce production costs; diversify into new markets, such as shrink, pouches or folding cartons; and add more value to their digitally printed labels through embellishments or special processes.’
Kevin Gourlay, senior vice president at Rotoflex, identifies important value-added finishes as PMS spot colors, varnishes, laminates, top coating, rotary screen, embossing, semi-rotary die-cutting, adhesives for cold or hot foil. High production speeds and fast job changeovers, and configurability and modularity ‘to expand capabilities as needed’, are additional considerations for Gourlay.
Efficiency
Gourlay’s colleague Artur Gondek, product and sales manager at Rotoflex Europe, has previously stated: ‘With shorter runs and a mix of digital and conventional label production, you need fast job changeovers.’
Running finishing in an off-line configuration can speed up the overall process, according to Gondek. ‘With high speed, highlyconfigurable off-line converting and finishing solutions, much like the DF3 that offers semi-rotary and full rotary QCDC (quick change die-cut) and flexo stations, you can accelerate the finishing process for a roll-to-roll digital press.’
The Rotoflex DF3 can adopt to quick changing jobs from inks to plates to dies – with 50 percent faster changeovers claimed – and shorten production times with speeds of 228m/min (750ft/ min). Customers have even shared examples of die changes that previously took 10-15 minutes now being changed in 30 seconds.
Labeltech general manager Gabriele D’Onofrio says: ‘The first request that customers demand is fast changeover, to help the just-in-time production required by digital printing.’
He continues: ‘As the discussion deepens, you realize that what customers really want is a low cost of interchangeable tools. Nowadays mostly all machines have a fast job set, but sometimes this will cause the tool cost to increase.’
AB Graphic has developed a new and improved version of its Fast Track Die semi-rotary die-cutting unit capable of running at up to 200m/min across a range of repeats. This, the company says, will enable customers to reduce the amount of finishing machines and overheads required when converting digitally printed materials.
Die-cutting at such higher speeds can present challenges with matrix stripping, which has led AB Graphic to develop a new system to overcome these issues and enable customers to run the machine consistently at highly productive levels.
‘Die-cutting to tolerance is a must,’ adds Schmitt. ‘A die-cutter platform must have software for distortion, scaling and registration to ensure all labels appear uniform.’
Daco has reengineered the shuttle system and rewrote some of the software to increase the speed of its range of semi-rotary die-cutting machines to enable higher production speeds.
The Daco DF350SR semi-rotary die-cutting unit uses a 20in RotoMetrics 176T magnetic die cylinder for semi-rotary applications with a useable repeat length of 8-22 inches, running at a speed of 65m/ min. The semi-rotary magnetic cylinder can be removed and replaced with rotary tooling from Daco or other manufacturers for full rotary applications, which pushes the production speed up to 175m/min. The flexo print/coating station (full rotary) utilizes servo drive technology, coupled with software written by Daco, to allow for quick and easy set-up. With the environment and paper costs in mind, the print-to-die register is accomplished with the use of very little substrate.
Bar Graphic Machinery’s (BGM) new Digiflex uses the very latest servo technology to ensure that accurate reregistration is maintained throughout all processes. A semi-rotary die station achieves ‘outstanding’ speeds while fully automated rapid slit system allows for precise positioning of slitting blades.
Efficiency focused developments at GM include: Smart Loading, an automatic flexible die plate changing system to reduce changeover times and to ensure an accurate die mounting in seconds; the Smart Stripping waste matrix stripping and rewinding system with servo-controlled tension, which sees the waste matrix peeled off around an idle rubber roller and immediately transferred to the rewinder; and Smart Crush, an ultra-quick set knives system allowing fast and precise setting of each crush knife even while running.
Further, GM sees one of the greatest tools for improving efficiency as laser die-cutting, offering zero changeover time and no die plate cost. It’s LC330 Compact Laser is an economic and fully digital laser finishing machine. It is set using the electronic file from the pre-press department. This ties in with GM’s vision for deeper JDF/JMF integration in the future, with the same data file used by different systems. Such deep integration with MIS will greatly facilitate and speed up the workflow in printing houses, proposes the company.
Smag Graphique has included increased workflow connection in the development of its new generation of finishing equipment. Refine Finishing has previously gone on record to state its view that software is integral to the development of hardware. Bjarke Nielsen, chief technology officer at Refine Finishing, says: ‘We often see technology colliding, where finishing built from a mechanical mindset is holding back the printing technology, which is increasingly software-driven. To maximize the printing capabilities, finishing should be as smart and as automated as possible.’
Diversification
Diversification as an umbrella topic has been ongoing in the label printing industry for a number of years. More recently, it has been realized with a growing number of narrow web printers and converters adding flexible packaging to their product mix. This includes those printed digitally, as in the case of UK printer CS Labels and its award-winning work with Xeikon’s dry toner technology.
Multilayer labels offer another new business opportunity. ‘They offer the perfect solution when the surface of a traditional self-adhesive label is not sufficient to communicate all information about the product,’ says Toksværd. ‘On the extra layers of the label you can put additional information about the product, add an advert or provide the information in several languages. Multilayer labels are often used for pharmaceutical and medical label applications – especially when government regulations require product information to remain intact with the product.’
Such applications and regulatory demands make digital an excellent tool to print such labels, typically produced in smaller batches, meaning the finishing equipment must be a match. CS Labels uses GM’s SmartLam module to convert digitally-printed peel and reveal labels. This undertakes lamination in register, as opposed to using a cross-over unit, meaning, the full web width is utilized. This doubles the production capacity and allows for full flexibility in the label design and size. GM’s in-line register unit is compatible with all GM DC330 modular finishing machines.
Grafotronic has recently introduced a version of its DCL2 modular converting machine for multilayer labels. This features the company’s new MLL module for multilayer labels featuring precise lamination.
As a caveat, Burton notes digital printing as being, potentially, a ‘very level platform’ that can make it difficult to diversify. However, he adds: ‘High end finishing solutions and creative techniques can give customers the diversification they need to stand out from the crowd.’
AB Graphic offers a number of finishing options for digitally printed packaging and labels, such as shrink sleeves, pouches and folding cartons.
Added value
These developments will be presented at Labelexpo Europe 2019 later this year, and include digital embellishment units for spot varnishes, cold foiling and tactile varnishes to add value to pre-printed labels.
A further development is new doming technology that combines low cost flatbed screen and hot foil technology. This is described by AB Graphic as ‘giving packaging converters the edge’ and producing ‘stunning results’.
‘Embellishments and special effects play an increasingly important role for manufacturers as they elevate a label design, adding the finishing touch to enhance the presentation of their brands,’ says Toksværd. ‘The techniques that our clients ask for are hot foiling, cold foiling, lamination, cast and cure, embossing, screen, and flood and spot coating.’
GM’s LC330 can be configured with flexo varnish, spot varnish, lamination, cold foil and automatic slitting stations. The company’s 330FB features screen printing, embossing and hot foil finishing. The DC330Mini and Miniflex label finishers can be equipped with flexo varnish, spot varnish, lamination, cold foil, die-cutting, automatic slitting and turret rewinder.
The flexographic print station of the BGM Digiflex can be used as a spot register/ flood coating station with the option of single or multiple colors using the automatic re-register multiple pass option. Additional options include cold foiling and a lamination unit. Daco’s DF350SR can be configured with an optional laminating station to give flexibility for digital finishing applications, and be used to apply spot or flood coat UV varnishes.
Smag expects growing demand for RFID to provide a boost for added-value processes. RFID-enabled products are used for marketing purpose, traceability and/ or logistic functions. With Smag having an established position in cosmetic and wine labels, it has now engineered dedicated converting technology for security labels, combining RFID insertion with data management. This has seen it partner with Avery Dennison and Nordic ID for an in-line option for inserting, encoding and control of RFID tags.
Modular
Schmitt identifies modularity as key to ensuring digital finishing systems grow with printers and the market. This is a ‘must’, he says: ‘You cannot go out and buy another finisher each time new opportunities evolve that require additional finishing capabilities. Adding a module simply, quickly and inexpensively is key.’
The Daco DF350SR is a fully modular system. Such flexibility enables a converting line to be configured for most digital finishing applications. An inkjet module is available, with systems from Inkjet Solutions and Domino recently fitted, as well as those from other manufacturers.
The BGM Digiflex is similarly fully modular, as are Grafotronic’s range of finishing lines. Lemorau has developed MEBR+ as a modular concept with a vast variety of configurations. EBRM+ is a simpler version of MEBR+. It is an affordable table-top digital finishing machine that can coat, die cut, slit and rewind digital printed webs.
Rotocontrol’s systems, such as the DT and RCF lines, rely on a modular construction, 100 percent servo-driven with individual module electronics to allow for easy add-on/future machine growth. Other notable elements include: semi-rotary or rotary die-cutting in the same module, reducing overall system length and cost; and a simple turret that can be integrated to allow for processing/handling of ganged production runs and multiple jobs produced on one roll, ‘not uncommon in the world of digital’, says Schmitt.
Smag is set to unveil a new modular and multi-process platform design at Labelexpo Europe 2019 that, combined with its automation experience through powerful servo high speed modules, will mean label manufacturers can take advantage of greater flexibility and reduced tooling costs. They can also achieve ‘comfortable’ running speeds and benefit from high-end value-adding modules for special effects like opacity, relief varnish and 3D effects.
DPR’s Virgo machines are compact finishing systems that offer modules for unwinding, lamination, knife cutting, waste matrix removal, slitting, and rewinding to finished rolls. DPR markets these as providing all the tools necessary to professionally cut and finish labels. The system uses cutting plotter technology to provide accurate label finishing. This allows different types of materials and shapes to be cut on the fly without the added cost of dies. This allows full flexibility and limitless variations in label design, the company notes.
Labeltech’s Stelvio system can be equipped with a flexo unit for varnish, spot varnish and cold foil, as well as a semi-rotary/rotary die-cutting unit, corona treatment, variable data printing, inspection, manual or automatic slitting unit, one or two rewinders, and semi-automatic turret rewinder.
Refine Finishing’s portfolio includes the Creative line of modular systems that can be tailored to the customer’s requirement, while Concept machines are fully customizable systems that are engineered on a project-by-project basis.
Prati’s Digifast One is a state-of-theart digital finishing machine processing at speeds of up to 80m/min. Available in L-R or R-L configurations, it can feature all of the options you’d expect, as well as inkjet for front and/or back printing.
Integration
In some instances, suppliers are capitalizing on modularity to integrate digital print and finishing technologies at a deeper level. A variation of the ‘hybrid’ phenomenon, largely realized by the combination of the flexo and inkjet print processes, such in-line configurations offer a number of benefits.
Smag has extend its collaboration with the main press manufacturers to propose finishing customization capabilities as standalone or integrated in-line hybrid systems. Grafotronic has recently hosted an open house in Poland, Digital Finishing Days, where it showcased its DCL digital finishing hardware configured as a hybrid line with Domino N610i UV inkjet printing technology.
The Gallus Labelfire combines digital inkjet printing and conventional processes such as flexo or screen. Labels can be varnished, laminated, embellished with cold foil and die-cut in a single operation. The conventional printing functions deliver additional finishing options and in-line processing like varnishing, laminating and die-cutting. A screen printing unit is fully integrated. A new option, digital embellishment Unit (DEU), can produce gloss and matte spot coatings and tactile relief effects in various thicknesses in a single pass.
‘In general, we see a growing demand for hybrid label presses for producing a variety of new label solutions and applications, for future narrow web application we might currently not even think of,’ comments Marx. ‘Brand owners are asking for more creative, luxury looks. A digital-only or flexo-only press is no longer good enough. With a hybrid press, like the Gallus Labelfire 340, label printing companies are able to meet exactly these demands: single pass printing, digital embellishment possibilities, short run flexibility, high print quality, the ability to produce new label applications and – maybe most relevant – the flexibility to react quickly to new market trends.’
The Rotocontrol RCF is a custom finishing line designed to support those investing in a hybrid press, offering in-line finishing and digital transport, booklet label production and more. It can be configured with: a second rewind station; rotary die-cutting; lamination; RFID and NFC label dispenser; RFID/NFC control and mark unit; web control with ultrasonic sensor for detection of transparent material; piece counter for transparent materials including holder; preparation friction shafts; laydown roller for winding shaft with pneumatic lifter; razor knife unit including three knife holders with blade; razor knife holder including blade; a 150mm rewind shaft; electronically regulated wastepaper rewind mounted on the machine; turret rewinder; core glue system; automatic core loader; and high-speed tail label roll closure system with printer.
Rotocontrol’s Schmitt says: ‘In-line and hybrid digital presses allow some or all of the processes required to be completed with just one pass and possibly just one machine operator. Shorter runs with complex set-ups usually provide label converters the highest dollar per label opportunity, but can be very costly to produce if multiple manpower and production cycles are required.’
‘A shared ultimate goal of both the brand owner and print providers is to get the label noticed. An absolute must is to create pizazz and elevate the label – this is where finishing enters the picture.’
Stay up to date
Subscribe to the free Label News newsletter and receive the latest content every week. We'll never share your email address.