Automate to survive
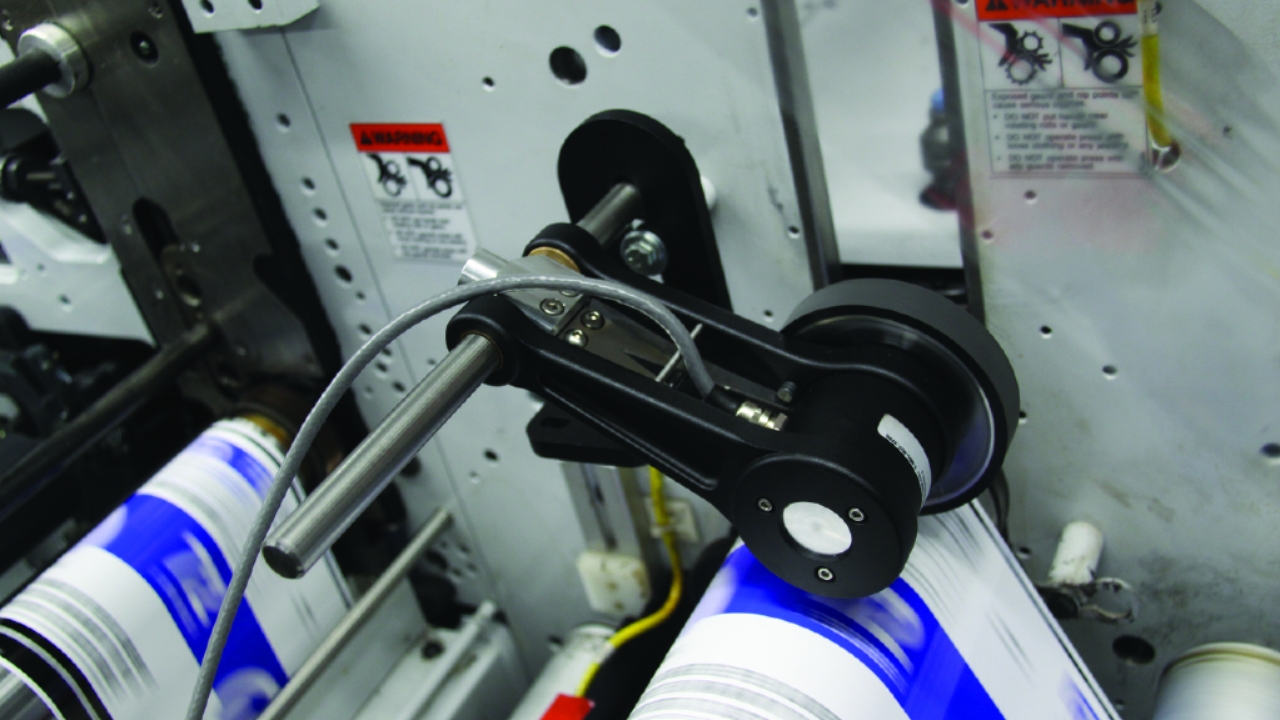
Being a label converter in the 21st century has undoubtedly come at one of the most demanding periods in the industry’s recent history. Run lengths are decreasing, lead times continue to get shorter, environmental and waste pressures continue to grow and quality demands increase.
Consequently, margins tend to get depressed and many converters have seen their profitability decline. Reports from many parts of the world indicate that a quarter to a third of label converters are in the caution or danger area in terms of financial viability. Not good news for the industry’s future.
However, there is much for the industry to celebrate when it looks ahead. Technology advances, new software solutions, E-commerce, the introduction of ‘Cloud’ computing and the ‘Internet of Things,’ together with an ever-faster rate of business integration and workflow automation, are all rapidly moving towards an industry that will be more streamlined, more automated, and more profitable in the future.
Part of the drive towards greater automation has initially come from the world of digital printing, where shorter run lengths and quick turn-rounds have created the need for enhanced pre-press automation, more sophisticated color management, ever-improving digital front ends (DFEs) and moves to integrated inspection and finishing. This, in turn, has now evolved into increasing automation of conventional analogue presses and processes.
Shorter run lengths and quick turnarounds also started to create bottlenecks in the business administration process, with more order processing, more demands on production scheduling, more demands on inventory control, and more invoicing. Today, all these stages are being integrated into increasingly sophisticated Management Information Systems (MIS) which fully integrate the whole administration process into one streamlined and automated workflow. This can be seen in the diagram below.
Information hub
MIS systems today enable everything from materials purchasing, to production, distribution, invoicing and accounts information to be held in one computerized system, integrating with other applications, including desktop productivity tools, press management control systems, inspection, finishing, inspection, accounting and administration systems and supply chain integration.
Systems are fully integrated so data only has to be entered once and changes ripple through to other modules automatically. For example, if a customer changes the quantity required on an order, the computerized system automatically adjusts the works order, re-times the job, adjusts the production schedule and stock control – and then re-calculates the quantity of raw materials allocated.
At the hub of an MIS system is a database that holds all the details required to manufacture, stock and sell the label or printed package products, including press requirements, tooling, colors/inks, plates and finishing. Materials order/stock modules include barcode-driven traceability and details of substrates. An origination module provides full control of design, proofing, platemaking, etc; the specification of the label drives the automated production planning process.
Modules used for job planning and production scheduling in the label or package printing plant are today an essential element of a MIS workflow system and can provide full visibility of machine capacity, both short and long term, and offer detailed scheduling of each production step of the job, from customer approval right through to shipping. Depending on the software it may also be possible for press operators to consult their work schedule on their press or feedback what they are actually doing. A change in schedule can be automatically seen on the shop floor.
Label and package printing production environments may change dramatically from one day to another, one shift to another, or even hour by hour. This means that the system needs to respond to the unexpected and quickly be able to identify backlogs and to modify existing production or press schedules. Flexibility in a system is therefore paramount. Keeping it simple makes scheduling manageable. Fast and responsive production scheduling is one of the major keys to successful supply-chain management, in some cases even linking customer’s and supplier’s schedules together.
Real time
Increasingly, MIS systems are starting to offer real-time feedback of shop floor activity to the scheduling board or screen via job tracking terminals or JDF capable systems. Others may look to define the current running efficiency as a resource for operators, or identify machine faults to automatically adjust running time of operations.
Some can provide an out of sequence alert, indicating jobs started early or not as planned, and so alerting the scheduler.
Outside of the main label and package printing MIS system, there are now an increasing number of print quality inspection, color, fault, barcode and other inspection solution available, both software and hardware - many of which (including AVT and AB Graphic) are already being integrated with Esko’s Automation Engine and MIS systems.
Esko’s Automation Engine serves as the heart of any pre-press production operation, integrating workflow automation with quality control. It comes with extensive business system integration capabilities and is highly scalable.
A job in Automation Engine represents a production order that organizes not only the data storage for the job, but also the job’s metadata – its link to order ID, due date, customer info, customer service representative contacts, etc. Besides these administration attributes, a job can also contain the graphics specifications like barcode, inks, RIP options. This job information can be used in any workflow to take advantage of all the data that is already there, avoiding double entries.
To meet the specific needs of digital printing in the label and narrow web markets AVT introduced Helios D, an automatic, 100 per cent print inspection system. Based on AVT’s Helios product line, Helios D supports all stages of digital production workflow, including the identification of specific defects like missing nozzles, ink dripping spots, and color changes as soon as they occur. The result is reduced waste, enhanced production and comprehensive process monitoring. The AVT systems extract business intelligence from the production floor and provide seamless connectivity to MIS and Automation Engine pre-press for optimized automated workflows.
Like some other quality control equipment and systems suppliers Global Vision has also embedded a Quality Control Platform within Esko’s Automation’s Engine so as to provide an all-in-one quality assurance system that runs as a background process and results in an annotated and viewable design file within Automation Engine. This further enables rapid and systematic review of all detected packaging and labeling errors throughout the workflow, from upstream design to print.
Color management
A highly adaptive new color management software technology for label and packaging applications is also available from QuadTech. Without any hardware modifications to the press, QuadTech’s ColorTrack software integrates with ink formulation software to simplify workflow and reduce the number of ink corrections needed to achieve accurate, optimal color.
Another software company with a product specific to the label industry is One Vision. The DigiLabel program automates label production workflows for digital label printers and combines print data optimization and production planning. DigiLabel operates throughout the entire production workflow: print data is automatically subjected to a quality control check and then optimized. The automated production of die-cutting forms or laser-cutting configurations, standard cut lines, a white background and the automatic dispatch of a release PDF to the customer for approval saves labor time and staff resources.
Some of the MIS systems available today also offer ‘Dashboards’. Dashboards make use of color, graphs, symbols, and charts to help users quickly and easily review critical management and financial data. This enables companies to take an immediate pulse of each department and quickly pinpoint problems. By combining data from throughout the MIS system, dashboards create a visual command center where it becomes possible to monitor company performance and launch profitable initiatives. Since getting to the root of an issue may require more than a glance, each Dashboard provides multi-level drilldowns. Each user of these systems can customize their dashboards by selecting from a list of available options that include cash position, net profit performance, late jobs, jobs due out each day, delivery by month, work-in-process analysis, sales metrics and underperforming employees. Although based on standard components, bespoke programming is often involved in tailoring individual MIS systems to an individual company’s needs. Modern MIS systems operate in real time, allowing the operator to move from window to window and enabling electronic commerce through flexible and adaptable architectures.
Automated presses
The label industry is continually seeking ways to further automate processes and press set-up and changeover information so as to remove the risks of human error.
Quite simply, the aim for the future – as Heidelberg puts it – is to work towards, ‘smart printing systems which will harness the power of digital integration to deliver new print systems and drive the industry forward.’ In short, to make printing presses (whether conventional or digital) that are self-managing, and where everything from production planning, to consumables ordering, to predictive maintenance, are all generated from the press itself.
Certainly, the use of scalable servo drive hardware with intelligent modular design press management software is already being used to minimize press set-up and make-ready, automate plate, cylinder or slitter changes, allow more consistent, repeatable results, and provide converter end-users with greater press flexibility. Inbuilt screens enable all the advanced controls to be visible alongside representative graphics, and provide for easier press commissioning and the simplification of fault finding. WiFi controlled automatic knife slitting has also recently been introduced.
All of this will have an increasing impact on press productivity, freeing up label companies to focus on developing their business rather than spending time on managing manufacturing. The use of cloud-based systems, where everything from press performance to planning scheduling is online and instantly available, will be part of the label world of tomorrow.
Integration with other software systems is also become ever more important, such as sales or corporate group accounting packages. Sales Cloud for example, is a software package that provides a complete view of customers, including activity history, key contacts, customer communications, lead management, sales forecasting, sales performance management and internal account discussions.
There are other domains that are typically not covered by MIS software. An example would be dedicated software for machine maintenance programs and/or for spare parts management.
Interfaces are also being created to more and more press DFEs which allow the automated creation of step-and-repeat profiles, and this capability is being built directly into digital presses, for example those from Xeikon and Screen.
Additionally, there are other domains that are sometimes not covered well enough by a ‘generalist’ MIS, such as a CRM (Customer Relationship Management) system – a tool which helps with contact management, sales management, productivity and more. The CRM within an MIS will likely do fine for ninety percent of label printers, but will not be good enough for a very sales-driven company. So, in these cases, MIS will need to create an interface to an external CRM. Another example that can be given is the payment of salaries.
Increasingly, MIS suppliers are also being asked to provide an interface so that electronic instructions can be sent to transport carriers, such as DHL and UPS, to manage transport. Cloud-based systems are also being used to automatically save every inbound and outbound e-mail against customer contacts and produce a sorted trail of previous discussions – all available in the right place when needed. It should be noted however, that integration with other software systems needs to be scalable and upgradable so as to avoid being stuck with the same MIS version forever.
Mobile options are also a hot topic in relation to the latest MIS systems, with management and sales personnel being enabled to access information or data through their mobile phones or tablets.
While this article has been designed to create a flavor of what is now taking place in the ongoing automation of the label and package printing sectors, a new handbook in the Label Academy series of titles will be published in the early New Year. Entitled ‘Management Information Systems and Workflow Automation,’ the book will provide an extensive overview of just what is now possible, and look at where automation developments are taking these sectors for the future – a human-free, 24/7, fully automated, workplace.
Even today, a sophisticated MIS system with efficient job planning and production scheduling capabilities is more than a nice-to-have tool; it is becoming a necessity.
This article appeared in the L&L Yearbook 2017, which can be read here
Stay up to date
Subscribe to the free Label News newsletter and receive the latest content every week. We'll never share your email address.