Who does what for my new digital press?
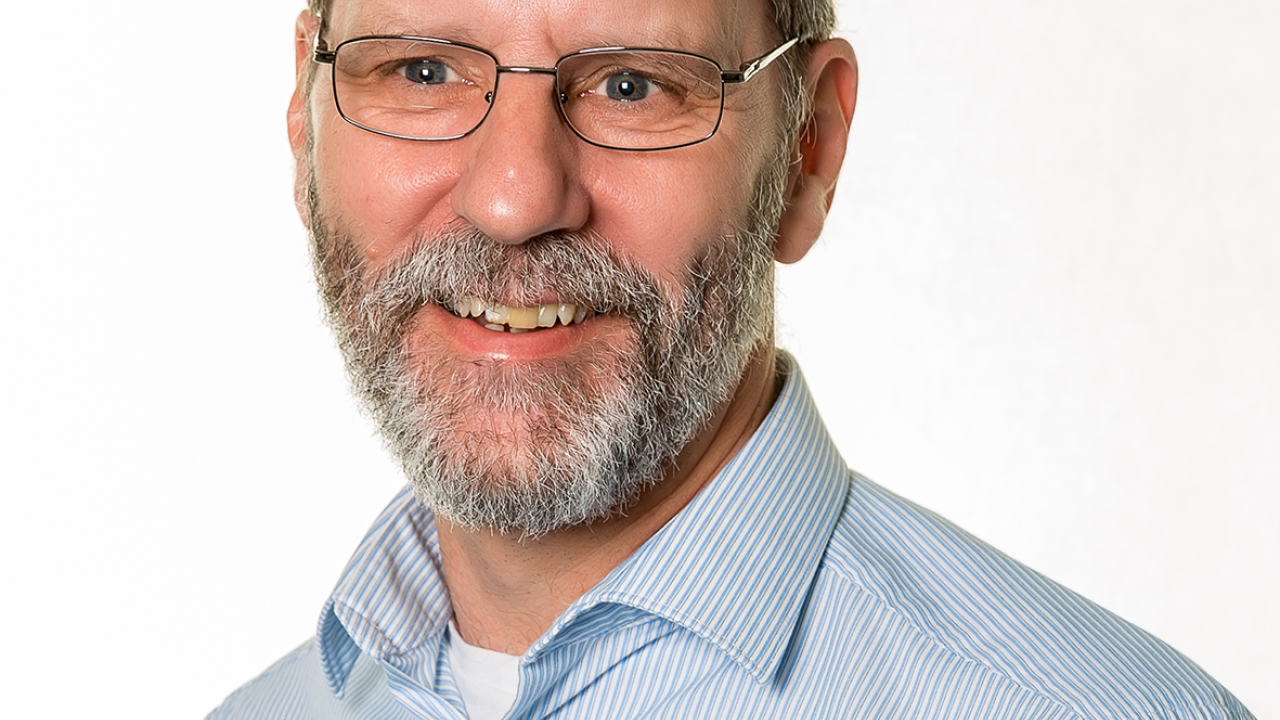
If you’re adding digital alongside your conventional presses you need to know how to drive it, but also to understand what the impact on your workflow and operator responsibilities will be. For your conventional press, your pre-press department takes your customers’ digital files (usually PDF) and creates plates from them. In that workflow they’re performing most of:
Preflight – checking that the files the customer submitted will print well. Checks may include minimum type sizes, minimum image resolution, etc.
Imposition – placing multiple labels as efficiently on the substrate as possible while maintaining compatibility with your finishing line and customer needs.
Color management – determining the ink set required and ensuring that files are specified correctly, or converting the job to use a fixed ink set (such as CMYK plus Orange, Green and Violet).
Trapping – ensuring that registration issues don’t cause artefacts in the printed result.
Rendering – converting from the images, strokes, fills and text of the PDF file to a raster format that the plate-setter can understand.
Screening or halftoning – converting the colors from continuous tone to the binary (ink or no ink) form that can be printed on press.
Plate-setting – making the plates that will be sent to the press room.
This conventional print workflow makes it easy to split processing and responsibilities between pre-press and press room; the interface between the two is the plate. Adding a digital press blurs the separation between pre-press and press room; PDF files must go all the way to the press.
In digital printing your plate is a PDF file. The PDF files are consumed by the Digital Front End (DFE), controller or RIP (Raster Image Processor), or even just the ‘workflow’.
So the input to the press room is not a plate any more, but a PDF file. The press operator role is very different from that in a conventional press room. Most of the same processes to be applied to the PDF are still required for digital, just as for conventional, but there are differences in what needs to be done in each step.
What’s the difference for digital?
Preflight is still required; you don’t want a job going to press unless the customer will be happy with the result. But think about why you’re investing in digital: if it’s to handle shorter run lengths that means that you must spend less time on each job. Manual steps in your process can damage profit margins. You need an automated preflight tool with manual review of any issues flagged.
Many DFEs offer preflight capability, but it’s often better done upstream, when the file is first received; telling a customer immediately that their file cannot be printed is preferable to when you’re right on their delivery deadline.
Imposition is also still required, but needs automating for the same reasons. If you’re migrating from narrow-web flexo to narrow web digital you may prefer to continue to use existing tools. Alternatively, most DFEs will offer this functionality.
Color management is the process that press operators will worry most about. The good news is that configuring color management on a digital press is significantly easier than for most conventional pre-press – once it’s set up properly. Almost all digital presses use a fixed ink set (eg CMYKOGV); the operator will often just need to tell the DFE which substrate is loaded and what resolution they’re printing at and the DFE will do the rest.
Some presses can be sensitive to temperature or humidity changes, so operators must respond to color drift, but vendors usually provide a pretty simple process to handle that. The techniques for maintaining stability on digital and conventional presses are different, but they’re equivalent in terms of complexity.
Trapping is rarely necessary for digital print. Digital registration is usually good and the ink on many inkjet presses spreads sufficiently to self-trap. This is good news: high quality trapping can be manual and time-consuming, and could eat into margins as run lengths and time on press for each job shorten. Rendering is still necessary – but is normally handled almost invisibly within the DFE once it’s been correctly set up.
Halftoning is also still necessary. The process of preparing jobs for flexo presses is painstaking, selecting the best screen for each graphical element to get flat colors, or smooth ends to vignettes. But digital presses are more like offset or gravure: it’s best to use a single screen for the whole job. That screen will normally be automatically selected for the media in use and the resolution that you’re printing at, like the color management.
I said a couple of times ‘this step is relatively straightforward once the DFE has been set up properly’, and that’s a key message. Setting up the DFE and operating it on a daily basis can, and often should, be treated as separate roles.
I recommend you have your vendor set up your press very carefully for your specific jobs, substrates and working practices, and then have them train your staff to be able to adjust it for new substrates. Once those configurations are locked in, using them is fairly simple. You will just need some capability to respond to unexpected variations from time to time.
Read this article in L&L issue 3, 2017, and here
See the L&L Digital Press Buyer's Guide here
Stay up to date
Subscribe to the free Label News newsletter and receive the latest content every week. We'll never share your email address.