★You are viewing this content as a subscriber
★Subscribers only
The role of coatings in the label value chain
Coatings are a critical part of the label value chain and have a multitude of functions
Coatings are a critical part of the label value chain with a multitude of functions beyond simple protection of the printed surface (see Figure 6.1).
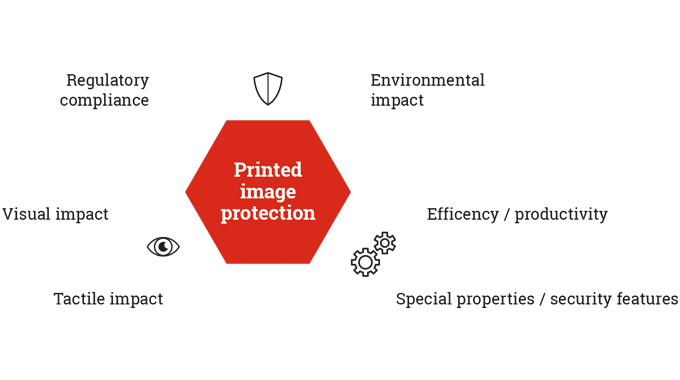
Stay up to date
Subscribe to the free Label News newsletter and receive the latest content every week. We'll never share your email address.