Choosing an MIS supplier
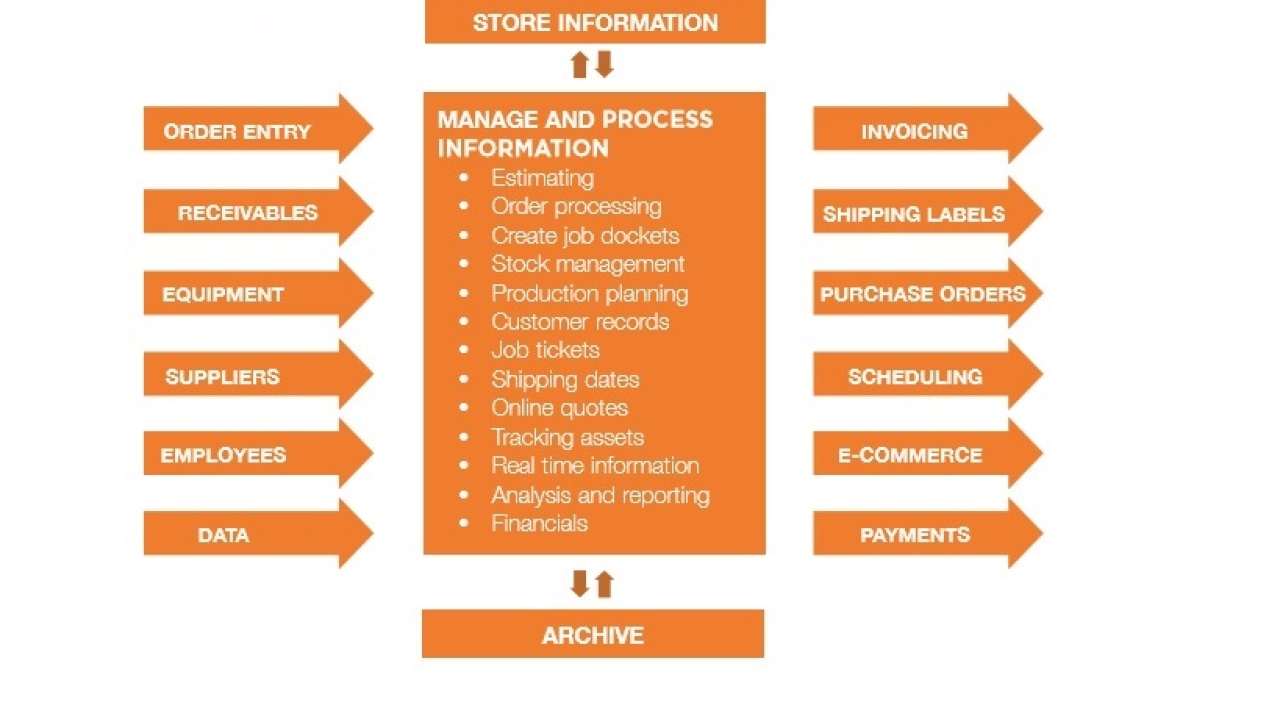
For those in a label or package printing business that are responsible for sourcing an MIS there will be a need to think carefully about what they want to achieve, especially on deciding where to best focus attention and on what areas of the business most require help or support to improve efficiency or performance.
Initially, a wish list of features – defined and written down – will need to be prepared as a starting point for talking with MIS and other specialized industry-related suppliers. This list needs to be broken down into categories (estimating, order processing, production management, inventory control, quality control, costing and accounting) in a way that can be given to potential suppliers.
The most successful installations will be the result of having clearly set out the company’s requirements and then both sides agreeing on exactly what is being supplied, when, and at what cost.
However, do not make the mistake of having too big a team to draw up the specifications; everyone will be asking for different (often conflicting) requirements and this can end up delaying implementation and maybe an over-specified and much more costly installation. Concentrate on the basics, but those which can be readily upgradable.
Key people in the company need to be involved in decision making, with the leadership staying involved, rather than looking to delegate the whole project. Make sure to use the vendor’s experience, use their training services as often as is required, and make sure that the project team meets on a regular basis.
It is important to choose an MIS supplier that understands the company’s specific industry sector needs (labels, cartons, sleeves, flexible packaging, etc) and that will support the company’s business through ongoing growth. Also ask about the quality of vendor support services: and whether the vendor is prepared to partner with other suppliers used by the business in, for example, inspection, pre-press, finishing. Ensure that they are always easily contactable. Queries need to be dealt with quickly.
Remember, the overall aim should be to end up with a single system that is able to manage the entire business, streamline the administration process and reduce costs, eliminate errors from the re-entry of data and minimize personnel.
Certainly the ease with which the MIS is able to integrate with other workflows such as those used by other market leaders that include Gallus, HP Indigo, Xeikon, Domino, Esko, AVT, AB Graphic, etc, is becoming increasingly important in providing a ‘joined-up’ workflow as seamless workflow automation continues to develop.
This opinion was published in L&L issue 4, 2017, and can be read online here
Stay up to date
Subscribe to the free Label News newsletter and receive the latest content every week. We'll never share your email address.