A challenging year ahead
After two years of pandemic restrictions, the industry has a new set of problems to face over the next 12 months.
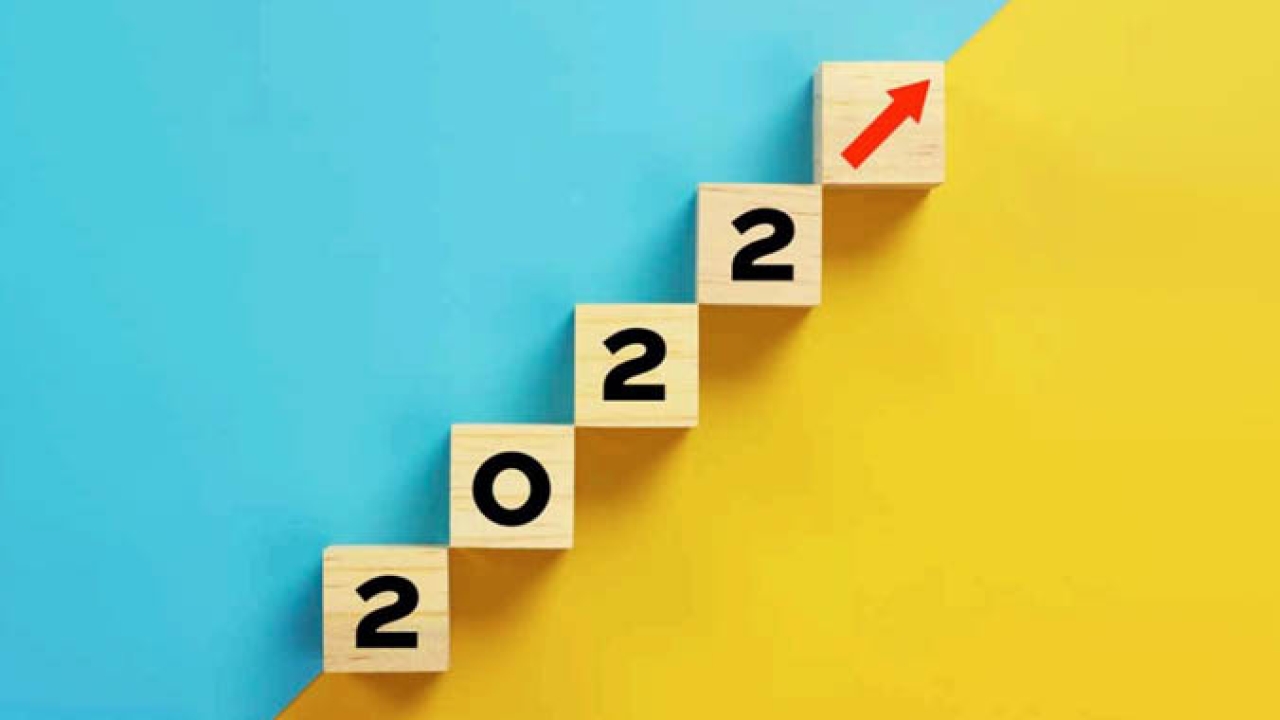
Just when the label industry thought it might be coming to the end of the, virtually global, Covid pandemic and the various lockdowns, the working from home restrictions, materials and labor shortages, supplier bottlenecks, extended supplier lead times, and cost and price increases, so along come another set of challenges that need to be faced and overcome – a war in Ukraine, even greater shortages of all kinds of products and materials, distribution problems, and rocketing energy prices, leading to inflation rates surging across the developed markets at a level not seen for many a long year.
Indeed, inflation was already running above target in the developed economies at the end of 2021, and that was before the Russia-Ukraine crisis which is bringing further inflationary pressures on commodity prices – particularly for energy and food – and a likely continuation of the supply chain disruption issues that the label industry has been facing during the past year. Agustin Carstens, the global central bank boss, expects policymakers may soon have to raise interest rates to levels not seen for many years.
These latest energy, commodity and inflationary factors are already having a major impact on not only businesses and households and the amount of money they have for investment and spending, but also on lifestyles, leisure, entertainment, household products, food and drink and, in turn, will undoubtedly have an increasing impact on the world of label and package printing – especially in the area of production, energy and investment costs over the coming months.
Leading international economic forecasters expect energy prices to remain high, possibly increase further, even if the war ends soon, and are already indicating that supply chain bottlenecks will tighten
due to sanctions and companies cutting ties with Russia, while Ukraine’s role in producing components for Europe’s automotive industry has already led to vehicle factory shutdowns in several eurozone countries.
Changes to food labels
Global food prices – already up by a third or more over the past year – are continuing to increase across Europe and the wider world. In particular, Russia and Ukraine are among the world’s leading producers of grain and sunflower oil. Indeed, Ukraine was exporting almost half of the world’s total supply of cooking oil before the conflict began. A significant reduction in supply of these products has impacted supermarkets and food manufacturers, both leading to rising costs and shortages of supply, as well as a possible need to adjust food product ingredients or cooking methods – and a subsequent need to reduce label run length orders and either increase food prices, reduce costs or change their labeling to reflect ingredients changes.
These latest energy, commodity and inflationary factors are already having a major impact
In this respect, perhaps some words of encouragement to label converters can come from the UK’s Food Standards Agency who have given temporary approval to substitute coconut oil, soybean oil, or fully refined palm oil in place of sunflower oil. It has also said that, given the ‘extraordinary circumstances’, manufacturers may also use rapeseed oil instead of sunflower oil and, at least for now, they will not have to print new labels or update their ingredient lists if they do make these substitutions. Hopefully other countries might make similar dispensations.
As a consequence of supply chain problems and cost increases, supermarkets and food manufacturers, who were already facing inflationary pressures of their own, are now being faced with consumer, and media, pressures on the rising cost of foods. What answers do they have? Try to cut costs? Minimize or simplify the product range? Reduce portion or pack sizes? Try and add value? If the label industry wants to minimize the possible impact of their key customers demanding cost cuts in the supply of labels and packaging, then they will likely have to spend more time working with them to find acceptable and new solutions.
Yet isn’t this what the label industry has always tried to do? It’s one of the reasons why label converters and industry suppliers have largely continued to achieve above inflation levels of growth for many years and, according to a recent Finat report, even continuing to attain quite good growth over the past Covid pandemic year and the problems that has created.
However, that continuing growth is now being countered by significant and persistent self-adhesive materials shortages that – if the Ukraine conflict continues without a successful resolution for any length of time – are likely to bring further supply chain disruptions during the second half of 2022.
So, what are the key issues and messages that the label industry needs to take on board to continue creating a profitable future?
Managing costs
Firstly, rising and high energy costs are not going to go away any time soon. They are a big part of label production, with presses, ancillary equipment, heating, lighting, offices and distribution costs being a key element of label pricing. But are all these factors now being adequately updated and accounted for in the label costing and pricing process. If not, they need to be looked at urgently. The same applies to materials costs. Are higher materials prices being incorporated into costing and accounting systems quickly enough when they occur?
Are there things that a label company can do to minimize or better manage manufacturing costs? Not leaving machines, computers, or electronic equipment on standby? Installing more energy efficient lighting? Provide lights that automatically turn off in cloakrooms, restrooms, warehouses, etc, when not actually in use? Turn off, remove or reduce lighting in non-essential areas? Maybe one or two degrees lower on heating thermostats, perhaps even installing a programmable ‘learning’ thermostat that will automatically adjust to the current temperature of the workplace and avoid energy wastage? Take advantage of off-peak periods wherever possible?
Regular cleaning and planned maintenance of electrical and mechanical equipment will undoubtedly optimize its performance and lifespan. Reduce the operating pressure of any air compressors and check for leakage and turn off when not in use. Another key point to consider is to make sure and involve the workforce, emphasizing the importance of reducing energy consumption. Explain that savings can benefit the whole company, enabling investment in new equipment that will makes factory life or jobs easier.
It would be nice to think that investment can be made from retained profits, but rising costs, inflation and squeezed margins will likely make this harder to achieve
Secondly, something which has not always been high on the must-have list when investing in new label machinery – energy-efficient equipment. Is the proposed investment designed to conserve energy? How does it compare with other makes or models? Does the manufacturer know what the energy usage of the machine is at different running or idling speeds? What is the optimum press performance? Maybe we will eventually get to the stage when label presses come with their own energy smart meters.
It has certainly been encouraging to note over the past year that a number of label press, ink curing and ancillary equipment suppliers have already been increasingly promoting energy saving and/or environmentally optimized capabilities, on-off functions to eliminate energy use in stand-by mode, or real-time data collection from hundreds of events per second to identify bottlenecks and optimize performance. Expect more of the same in the coming year.
The same kind of approach should be applied to minimizing waste. Optimum handling and storage of labelstock needs to be emphasized to reduce materials wastage before it even gets to the press. Effective and efficient press set-up, better press management, the latest control and label inspection systems, accurate label counts, and careful handling, storage and packing of finished rolls, can all have an impact on reducing productions costs.
Thirdly, what impact will rising interest rates and high inflation have on the label and packaging industry? Certainly, any label converter or industry supplier looking to borrow money for a major investment can expect steadily rising interest rates over the coming year, probably even longer, bringing with it a decreasing purchasing power. It would be nice to think that investment can be made from retained profits, but rising costs, inflation and squeezed margins will likely make this harder to achieve.
Prepared
A further impact of inflation is that most materials and labor will increase in price, in which case the label business will need to charge accordingly to stay afloat. This will mean assessing the goods and services that bring in business the most and the least in value. Noting what competitors are doing. Always have an emergency plan. It is best to be prepared.
To add a word of support and encouragement, the label industry has seldom achieved annual growth below GDP, even during the most difficult of times. It continued to grow last year, and is expected to achieve growth again in 2022 – but few forecasters expect life to be easy. But, as Gloria Gaynor might sing, ‘We will survive.’
Stay up to date
Subscribe to the free Label News newsletter and receive the latest content every week. We'll never share your email address.