Formalizing an education and training program for the worldwide label industry
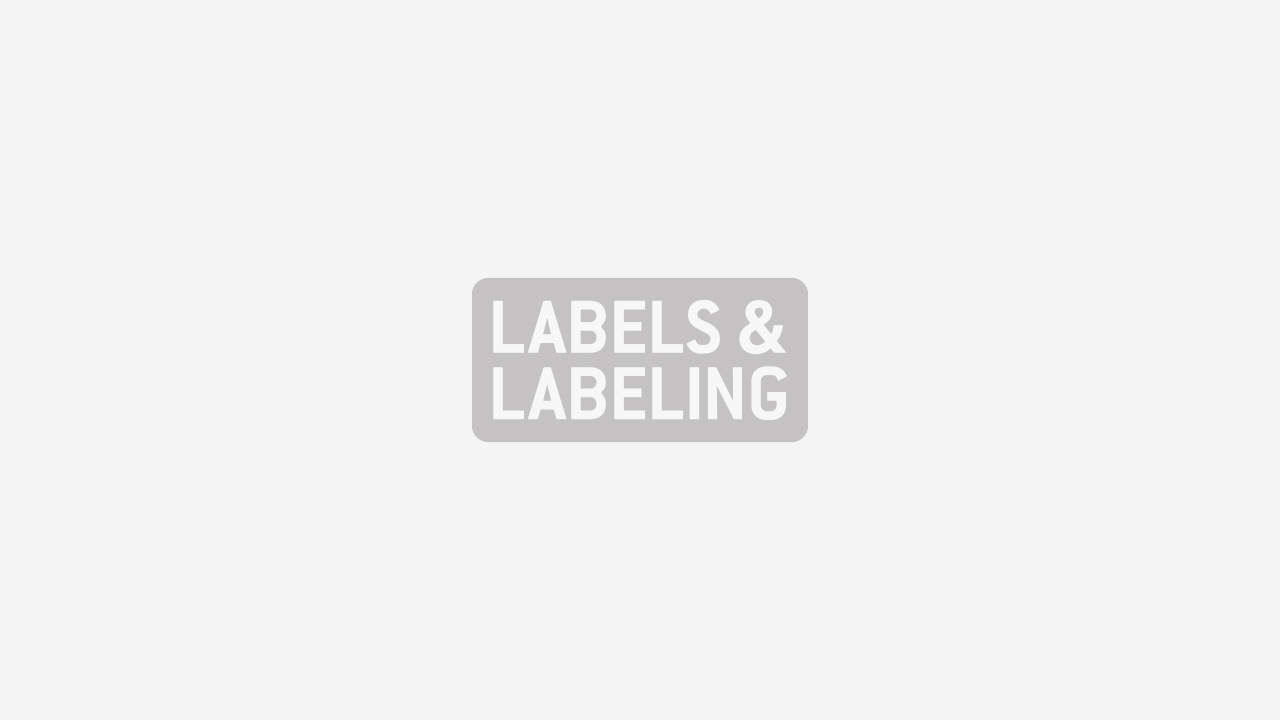
For the past three years Labels & Labeling has undertaken industry surveys in all the key markets where it organizes exhibitions, summits or conferences. In virtually every market surveyed to date, education and training is identified as one of the main industry needs required to stimulate further growth and development of the industry for the future whether it is for an existing and well established label market such as Europe or North America, or in the newer, emerging markets of the world such as India, China, Latin America, Eastern Europe or South East Asia.
Interestingly, this need for education and training does not come from a lack of knowledge in the industry, but more from a lack of any formalized international education and training programs or systems that label companies can easily adopt, follow and implement so as to have a global education and training system.
Such a system would enable any label-related company - whether an industry supplier or converter - to follow, say, a series of education and training modules that would formalize and track the development of every employee in the industry, wherever they are employed and in any country. Modules like this would utilize internal company personal to pass on knowledge and skills, monitor and sign off stages of training, so enabling every person entering the industry to have a logbook that records and monitors their development and progress. These logbooks would be transferable between companies and sections of the industry and could follow each employee throughout his working life if required.
Existing external training resources such as schools and colleges, industry training centers, supplier training and technology facilities, conferences, seminars and workshops, can all still be utilized with the logbook scheme, signing off modules as education and training takes place. Visits to paper mills, film extruding plants, adhesive coaters, ink makers, packaging companies, label users, etc, can also be incorporated into the training program - but now in a more formalized manner.
It is to provide this global education resource, with a standardized system of modules, encompassed into an employee's individual training logbook, that an outline industry training program is being developed. Designed by renowned label industry expert Mike Fairley, it is based on his near 40 years of experience in education, industrial training, courses, seminars, workshops and in-house presentations, visits to converters and suppliers, and from undertaking all the survey analysis. This initial basic program being created is being based on 20 identified modules.
The basic module approach
In order to create a global approach to education and training, the main basic level knowledge and skills needed to grow the industry and develop individuals has initially been proposed as being divided into 20 modules, each covering a particular aspect of knowledge requirement or industry sector; for example, label materials, label printing processes, inks, pre-press and plates, etc. Not all employees will follow all modules; only those most relevant to their particular job or department, but these can be added to as training or responsibilities grow.
On joining a company the new employee would sit with the person or persons allocated the responsibility for their development and go through the modules to build up a specific training program. This might commence with just one module, or even one part of a module. The responsible human resources or training manager, department manager, supervisor, etc, would then monitor and sign off the training topics and modules as the employee progresses.
The range of basic modules currently identified is:
Module 1 - Label history, label types and label technology solutions
Module 2 - Labels substrates, adhesives, liners and coatings
Module 3 - Origination, pre-press, plates and proofing
Module 4 - Mechanical label printing process and techniques
Module 5 - Inks, coatings, varnishes and ink drying technologies
Module 6 - Dies, die-cutting, tooling and web finishing technologies
Module 7 - Tension, register and other print quality and web inspection systems
Module 8 - Label application technology, labeling systems and print apply solutions
Module 9 - Methods and techniques of electronic printing using impact and non-impact systems
Module 10 - Codes and coding technology
Module 11 - Digital printing technology and applications
Module 12 - Label properties, terminology, testing, test equipment and procedures
Module 13 - Security, smart and intelligent materials, techniques and procedures
Module 14 - Global organizations, standards and regulations
Module 15 - International measurement systems and conversion
Module 16 - Computer terminology and applications used in the label industry
Module 17 - Management issues, techniques and procedures
Module 18 - Label end-user applications and markets
Module 19 - Special label, ticket and tag constructions
Module 20 - Training and training organization
It is to be hoped that industry suppliers, current industry training organizations and associations would consider sponsoring individual modules to enable them to be kept to low cost so that all sizes of converters can afford to encompass the training scheme.
At a later stage, or maybe in tandem, a more advanced series of modules could be developed and introduced, with perhaps a more practical, operator level, content. For example, the basic module on mechanical label printing processes might be divided into more advanced and more intense modules separately covering: flexography, letterpress, offset, screen process, hot foil, etc. Indeed, individual press manufacturers might create modules for their own specific technology and build this into the overall system.
Similarly, the main labelstock suppliers might consider developing advanced modules which specifically cover filmic materials, synthetic materials, paper-based materials or VIP materials. These should be easy to integrate into the global education and training scheme.
How to use the training modules
Once a module or modules have been allocated, the employer should review the specific topics or subjects within each individual module with the specific employee. Much of the initial knowledge content can be found within the label industry's key reference source - the Encyclopedia of Labels and Label technology. This can be supplemented by other industry publications and books, through supplier literature, through internet searching, and through talking, discussion and training briefings with senior or other specific experienced company employees.
It is suggested that each topic or subject could take at least one to four weeks of study before any testing and signing off of the knowledge takes place. Re-testing may sometimes be necessary if the employee does not appear to have attained a sufficient knowledge level. Where external training, courses, workshops, supplier activities are incorporated, then the appropriate course tutor or presenter may wish to sign off attendance at these events.
It is anticipated that the module program would be integrated into existing company recruitment, development and appraisal systems.
How would the program be administered?
Within the development of a global education and training program for the industry it is proposed that, because of its international resources, Tarsus should write, publish and make available the initial sets of 20 training modules - possibly sponsored by some of the leading global international supplier organizations to keep module costs for user companies to a manageable level. This would ideally be in co-operation with FINAT, TLMI, LATMA, LMAI, SALMA, JFLP and other associations and whose education and training committees would advise on subject coverage, review module content and approve completed modules for publication.
Modules would be supplied in some form of long-lasting loose leaf binder that trainees would be able to add to, collect notes or samples in, etc. Marketing of the modules to the industry would be through the Tarsus global website, Labelexpo shows and Summits and Labels & Labeling.
The role of the various association education and training bodies would be to act as overall administrators of the scheme in their respective region(s) of the world, including the accreditation of training individuals, training organizations, colleges or schools, supplier company trainers and approved instructors, and the issuing of accreditation certificates and logos that training bodies could use in their own material, promotion, marketing, etc. A modest fee might be payable to the association by each relevant organization seeking accreditation for this approval, accreditation and certification process.
Each association may also consider the issuing of certification to industry trainees that complete the basic course of industry education and training modules, together with a handbook of accredited training organizations, individuals, colleges, etc, which could be compiled an issued by the associations each year.
As a second, later, stage, it is suggested that an advanced set of education and training modules should be developed for trainees that wish to progress to more senior levels in the industry. Sales, management and other specialist areas might also be incorporated into the global scheme. In all cases, the associations would act as the accreditation and certification bodies.
A further area of consideration for associations is the possible establishment and running of short courses, workshops, etc, to meet the objectives of specific modules. In practice, to become one of the accredited training organizations and be able to run short courses and charge fees for these courses.
The end result of developing a global training scheme would be:
- To create a total global industry scheme adopted by all the main industry associations
- To develop and raise industry education and training standards
- To approve and accredit trainers and training organizations in each region
- To raise the profile and membership of the associations through their role in industry training
- To enhance association income through administration and accreditation processes and the running of short courses
- To aid the industry in having a greater knowledge of methods and techniques for enhancing quality, performance, and added value
- To improve job satisfaction and self-worth of employees through improved job training
Feedback on this concept of a global education and training scheme for the label industry would be welcomed. It is something that appears to be badly needed, would be of considerable benefit to the industry and would raise standards for the future. If the industry really wants such a scheme it can be up a running in under a year.
Let's have your thoughts and comments on the proposal.
Stay up to date
Subscribe to the free Label News newsletter and receive the latest content every week. We'll never share your email address.